МЕТАЛЛООПТИКА, раздел оптики, в к-ром изучается взаимодействие
металлов с электромагнитными волнами. Осн. оптич. особенности металлов: большой
коэфф. отражения R (напр., у щелочных металлов R ~ 99% ) в
широком диапазоне длин волн и большой коэфф. поглощения (электромагнитная волна
внутри металла затухает, пройдя слой толщиной 6~ 0,1 -т- 1-10-5 см,
см. Скин-эффект). Эти особенности связаны с высокой концентрацией в
металле электронов проводимости (см. Металлы).
Взаимодействуя с электромагнитной волной, падающей на поверхность металла,
электроны проводимости одновременно взаимодействуют с колеблющимися ионами
решётки. Осн. часть энергии, приобретённой ими от электромагнитного поля,
излучается в виде вторичных волн, к-рые, складываясь, создают отражённую волну.
Часть энергии, передаваемая решётке, приводит к затуханию волны внутри металла.
Электроны проводимости могут поглощать сколь угодно малые кванты
электромагнитной энергии hw (h - Планка постоянная, w - частота
излучения). Поэтому они дают вклад в оптич. свойства металла при всех частотах.
Особенно велик их вклад в радиочастотной и инфракрасной областях спектра. По
мере увеличения со вклад электронов проводимости в оптич. свойства металлов
уменьшается, уменьшается и различие между металлами и диэлектриками.
Остальные валентные электроны влияют на оптич. свойства металла только когда
они участвуют во внутр. фотоэффекте, что происходит при hw >
ДE (ДE - энергетич. щель между основным и возбуждённым
состояниями электронов). Возбуждение электронов приводит к аномальной дисперсии
волн и к полосе поглощения с максимумом вблизи частоты резонансного поглощения.
Благодаря сильному электрон-электронному и электрон-ионному взаимодействию
полосы поглощения в металле значительно шире, чем в диэлектрике. Обычно у
металлов наблюдается несколько полос, расположенных гл. обр. в видимой и
ближней ультрафиолетовой областях спектра. Однако для ряда поливалентных
металлов наблюдаются полосы и в инфракрасной области спектра. При частотах w
>= w п, где w п - плазменная частота валентных электронов, в металле
возбуждаются плазменные колебания электронов. Они приводят к появлению области
прозрачности при w = wп.
В ультрафиолетовой области коэфф. отражения R падает и металлы по
своим свойствам приближаются к диэлектрикам. При ещё больших частотах
(рентгеновская область) оптич. свойства определяются электронами
внутренних оболочек атомов и металлы по оптич. свойствам не отличаются от
диэлектриков.
Оптич. свойства металлов описываются комплексной диэлектрической прони-
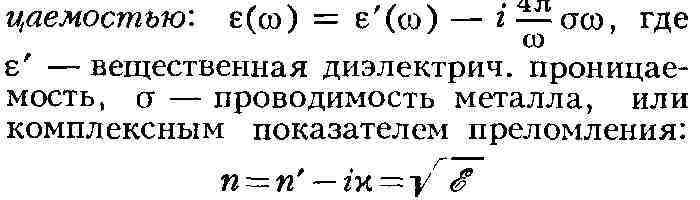
(и - показатель поглощения). Комплексность показателя преломления выражает
экспоненциальное затухание волны внутри металла. При падении плоской волны на
поверхность металла под углом ф не= 0 волна внутри металла будет неоднородной.
Плоскость равных амплитуд параллельна поверхности металла, плоскость равных фаз
наклонена к ней под углом, величина к-рого зависит отер. Волны, отражённые от
поверхности металла, поляризованные в плоскости падения и перпендикулярно к
ней, имеют разность фаз. Благодаря этому плоскополяризованный свет после
отражения становится эллиптически-поляризованным. Коэфф. отражения R волн,
поляризованных в плоскости падения, у металлов, в отличие от диэлектриков,
всегда не= 0, и лишь имеет минимум при определённом ср.
Для чистых металлов при низкой темп-ре в длинноволновой области спектра
длина свободного пробега электронов i становится >о. При этом
затухание волны перестаёт быть экспоненциальным, хотя и остаётся очень сильным
(аномальный скин-эффект). В этом случае комплексный показатель преломления
теряет смысл и связь между падающей и преломлённой волной становится более
сложной. Однако свойства отражённого света при любом соотношении между i и о
полностью определяются поверхностным импедансом Z, с к-рым связывают
эффективные комплексные показатели поглощения и преломления:

Для измерения и и и массивного металлич. образца исследуют свет, отражённый
от его поверхности, либо поляризационными методами (измеряются характеристики
эллиптической поляризации отражённого света), либо методами, основанными на
измерении R (в широком спектральном диапазоне) при нормальном падении
его на поверхность металла. Эти методы позволяют измерить оптич. характеристики в инфракрасной, видимой и ультрафиолетовой областях с ошибкой
~0,5-2%. Для измерения тонкой структуры полос поглощения используются методы,
основанные на модуляции свойств металла, приводящей к модуляции интенсивности
отражённого света, к-рая и измеряется (термоотражение, пьезоотражение и т.
п.). Указанные методы позволяют с большой точностью определить изменения R при
изменении темп-ры, при деформации и т. п. (см. табл.),
Оптические характеристики некоторых металлов
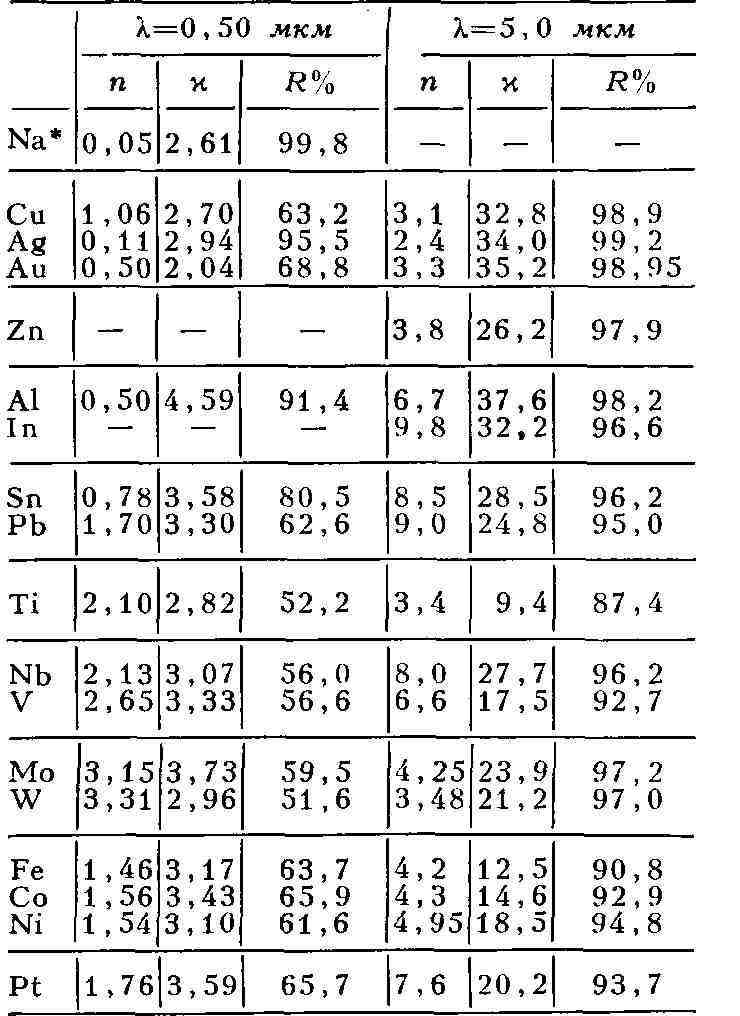
* Оптические характеристики относятся к X=0,5893 мкм.
а также исследовать тонкую структуру полос поглощения. Особое внимание
уделяется приготовлению поверхности исследуемых образцов. Поверхности нужного
качества получаются электрополировкой или испарением металла в вакууме с
последующим осаждением его на полированные подложки.
М. позволяет по оптич. характеристикам, измеренным в широком спектральном
диапазоне, определить основные характеристики электронов проводимости и
электронов, участвующих во внутреннем фотоэффекте. М. имеет также и прикладное
значение. Металлические зеркала применяются в различных приборах, при
конструировании к-рых необходимо знание R, n и % в различных
областях спектра. Измерение п и х позволяет также
установить наличие на поверхности металла тонких плёнок (напр., плёнки окиси) и
определить их оптич. характеристики.
Лит.:
Соколов А. В., Оптические свойства металлов, М., 1961; Борн М.,
Вольф Э., Основы оптики, пер. с англ., М., 1970; Гинзбург В. Л., М о т у л е в
и ч Г. П., Оптические свойства металлов, "Успехи физических наук",
1955, т. 55, в. 4, с. 489; Мотулевич Г. П., Оптические свойства поливалентных
непереходных металлов, там же, 1969, т. 97, в. 2, с. 211; Кринчик Г. С.,
Динамические эффекты электро- и пьезоотражения света кристаллами, там же, 1968,
т. 94, в. 1, с. 143; Головашкин А. И., Металлооптика, в кн.: физический
энциклопедический словарь, т. 3, М., 1963.
Г.
П. Мотулевич.
МЕТАЛЛООРГАНИЧЕСКИЕ СОЕДИНЕНИЯ, органические соединения, содержащие
атом к.-л. металла, непосредственно связанный с атомом углерода.
Все М. с. можно подразделить на две группы: 1. М. с. непереходных и часть М.
с. переходных металлов. Эти соединения содержат одинарную (а) связь металл - углерод.
2. М. с. переходных металлов (в т. ч. карбонилы металлов), построенные
путём заполнения $-, р- и d-орбиталей атома металла я -электронами
различных ненасыщенных систем, напр, ароматических, олефиновых, ацетиленовых,
аллильных, циклопентадиенильных.
Из М. с. 1-й группы наиболее полно изучены производные Li, Na, К, Be, Mg,
Zn, Cd, Hg, B, Al, Tl, Ge, Sn, Pb, As и Sb. Свойства этих соединений
определяются характером связи М-С (М - атом металла), зависящей гл. обр. от
природы металла, а также от характера и числа органич. радикалов, связанных с
атомом металла. В М. с. щелочных металлов связь М-С сильно поляризована, причём
на атоме металла сосредоточен частичный положительный, а на атоме углерода -
частичный отрицательный заряд: М+--С-. Поэтому такие М. с. весьма
реакционноспособны: они энергично разлагаются водой и очень чувствительны к
действию кислорода. Практически их используют только в растворах (углеводороды,
эфир, тетрагидрофуран и др.), защищая от влаги, СО2 и кислорода
воздуха. Аналогичные свойства присущи соединениям щёлочноземельных металлов
(Mg, Ca), а также Zn, Cd, В и А1. Напр., такие вещества, как (CH3)2Zn,
(СНз)зВ, (С2Н5 )3А1, воспламеняются на
воздухе. Более стабильны смешанные М. с. этих элементов, в к-рых металл связан
с органич. радикалом и с 1 или 2 кислотными остатками, напр. (С2Н5)2А1С1,
С2Н5 А1С12. С возрастанием
электроотрицательности металла полярность связи М-С уменьшается, и соединения
таких металлов, как Hg, Sn, Sb и т. п., по существу кова-лентны. Это
перегоняющиеся жидкости или кристаллич. вещества, устойчивые к действию
кислорода и воды. При нагревании они распадаются с образованием металла и
свободных органич. радикалов, напр.: (С2Н5)4РЬ -> РЬ +
4С2Н5
М. с. 1-й группы могут быть получены взаимодействием металлов с галогенал-килами
(или галогенарилами):
H-C4H9Br+2Li -> H-C-iHuLi + LiBr присоединением
гидридов или солей металлов по кратной связи:
ЗСН2=СН2+А1Н3 -> <С2Н5)3А1
взаимодействием диазосоединений с солями металлов:
2CH2N2+HgCl2 -> ClCH2HgCH2Cl
+ 2N2взаимодействием М. с. с галогенидами металлов, металлами и друг
с другом:
3CeH5Li+SbCl3 - (C6H5)3Sb
+ 3LiCl
(C2H6)2Hg+Mg -> (C2H5)2Mg+Hg
(CH2=CH)4Sn+4CeH6Li -> (CeH5)iSb++ 4CH2=CHLi.
М. с. переходных металлов, относящиеся к 1-й группе, склонны к гомолитическому
распаду (алкильные производные Ag, Си и Аи); арильные и алкенильные соединения
этих элементов более стабильны, очень прочны ацетилениды, а также метальные
соединения платины, напр. (СНз)зРИ и (CH3)4Pt.
В М. с. 2-й группы атом металла взаимодействует со всеми атомами углерода
я-электронной системы. Типичные представители этого класса М. с.- ферроцен,
дибензолхром, бутадиен-железо-три-карбонил. Для соединений этого типа,
полученных сравнительно недавно, классич. теория валентности оказалась
непригодной (об их электронном строении см. Валентность).
М. с. сыграли большую роль в развитии представлений о природе химической
связи. Их используют в органич. синтезе, особенно литийорганические
соединения и магнийорганические соединения. Многие из М. с. нашли
применение в качестве антисептиков, лекарственных и физиологически активных
веществ, антидетонаторов (напр., тетраэтилсвинец), антиокислителей, стабилизаторов
для полимеров и т. д. Очень важно получение чистых металлов через карбонилы и
М. с. при произ-ве полупроводников и нанесении металлопокрытий. М. с.-
промежуточные вещества в ряде важнейших пром. процессов, катализируемых
металлами, их солями и комплексными ме-таллоорганич. катализаторами (напр.,
гидратация ициклополимеризация ацетилена, анионная, в том числе и
стереоспецифическая, полимеризация олефинов и диенов, карбонилирование
непредельных соединений). См. также Алюминийорганические соединения,
Мышьяк-органические соединения, Сераорганические соединения,
Сурьмаорганические соединения, Цинкорганические соединения, Гринъяра реакция,
Несмеянова реакция, Кучерова реакция, Вюрца реакция, Переходные элементы,
Ферроцен, Полимеризация.
Лит.:
Химия металлоорганическнх соединений, под ред. Г. Цейсса, пер.
с англ., М., 1964; Р о х о в Ю., X е р д Д., Л ь ю и с Р., Химия
металлоорганических соединений, пер. с англ., М., 1963.
Б. Л. Дяткин.
МЕТАЛЛОПЛАСТ, листовой конструкционный материал, состоящий из метал
-лич. полосы (листа) и полимерной плёнки, нанесённой с одной или двух сторон.
Толщина металлич. полосы обычно 0,3-1,2 мм, полимерной плёнки 0,05-1 мм.
Для изготовления М. пригодно большинство листовых конструкц. металлич.
материалов (сталь, алюминий и его сплавы, титан и др.). Плёнка может быть из
полиолефинов, фторопластов, полиамидов, пластифицированного поливинилхлорида и
др. полимеров. М. получают путём наклеивания на металлич. полосу заранее
изготовленной плёнки, погружением полосы в расплав полимера, нанесением
полимерной пасты или напылением полимера в порошкообразном состоянии (см.
Напыление полимеров). Покрытие может быть одно- или многоцветным, гладким или
рельефным, имитировать ценные породы дерева, мрамор и др. материалы. М. не
расслаивается в процессе деформации металла при штамповке, гибке или вырубке.
Изделия не нуждаются в антикоррозионной защите и декоративной отделке.
М. впервые получен в нач. 40-х гг. 20 в. в Германии. Применяют в стр-ве для
отделки зданий, перил балконов, крыш, водосточных желобов, внутр. обшивки стен,
изготовления дверных и оконных рам, а также для произ-ва корпусов автомобилей,
холодильников, стиральных машин, радиоприёмников, телевизоров, тары для
хранения агрессивных материалов, для внутр. отделки салонов пассажирских
самолётов, вагонов, автофургонов и т. д.
Лит.:
Минченок Н. Д., Шумная В. А., В е р н и к Р. А., Производство
рулонного проката с полимерными покрытиями, "Лакокрасочные материалы и их
применение", 1969, № 5; П о л я к о в а К. К., 3 е л ь ц е р Ю. Г.,
Полимерные покрытия полосового проката, М., 1971.
А. А. Черников.
МЕТАЛЛОПРОТЕИДЫ, класс сложных белков; представляют комплексы
белков с ионами металлов. Связь между белком и металлом (Fe, Cu, Zn, Mg, Mn, V,
Mo и др.), как правило, непрочна, однако удаление металла (напр., разбавленными
неорганич. к-тами) приводит к нарушению строения и функциональных свойств М.
Распространены в живой природе и выполняют важные биол. функции: транспорт
кислорода у беспозвоночных (гем эритрин, гемоцианин), депо и транспорт
железа (ферритин, трансферрин), депо и транспорт меди (церулоплазмин) и
др. К М. относятся мн. ферменты (нек-рые пептидазы, тирозиназа, оксидаза
аспарагиновой к-ты и др.).
Лит.:
Гауровиц ф., Химия и функции белков, пер. с англ.. М., 1965;
Северин С. Е., Филиппов П. П., Кочетов Г. А., Металлоанзнмы, "Успехи
современной биологии", 1970, т. 69, в. 2; V а 1 1 е е В. L., W а с k с r
W. Е. С., Metalloproteins, в кн.: The proteins, ed. H. Neurath, v. 5, N. Y. -L., 1970.
МЕТАЛЛОРЕЖУЩИЙ ИНСТРУМЕНТ, орудие производства для изменения формы и
размеров обрабатываемой металлич. заготовки путём удаления части материала в виде
стружки с целью получения готовой детали или полуфабриката. Различают станочный
и ручной М. и. Осн. части М. и.: рабочая, к-рая может иметь режущую и
калибрующую части, и крепёжная. Режущей наз. часть М. и., непосредственно
внедряющаяся в материал заготовки и срезающая часть его. Она состоит из ряда
конструктивных элементов: одного или неск. лезвий; канавок для отвода стружки,
стружколомателей, стружкозавивателей; элементов, являющихся базовыми при
изготовлении, контроле и переточках инструмента; каналов для подвода
смазочно-охлаждающей жидкости. Назначение калибрующей части -восполнение
режущей части при переточках, окончательное оформление обработанной поверхности
и направление М. и. при работе. Крепёжная часть служит для закрепления М. и. на
станке в строго определённом положении или для удержания его в руках и должна
противодействовать возникающим в процессе резания усилиям. Крепёжная часть
может выполняться в виде державок, хвостовиков (вставные М. и.) или иметь
отверстие для крепления на оправках (насадные М. и.).
В зависимости от технологич. назначения станочный М. и. делится на следующие
подгруппы: резцы, фрезы, протяжки, зуборезный, резьбонарезной, для
обработки отверстий, абразивный и алмазный инструмент. Резцы, применяемые на
токарных, токарно-револьверных, карусельных, расточных, строгальных, долбёжных
и др. станках (за исключением резьбовых и зуборезных резцов), служат для
обточки, расточки отверстий, обработки плоских и фасонных поверхностей,
прорезания канавок. Фрезы - многолезвийный вращающийся М. и. используют на
фрезерных станках для обработки плоских и фасонных поверхностей, а также для
разрезки заготовок. Протяжки - многолезвийный инструмент для обработки гладких
и фасонных внутренних и наружных поверхностей. Для образования и обработки отверстий
используют свёрла, зенкеры, зенковки, развёртки, цековки, расточные
пластины, комбинированный инструмент, к-рый применяют на сверлильных, токарных,
револьверных, расточных, координатно-расточных и др. станках. Зуборезный
инструмент предназначен для нарезания и обработки зубьев зубчатых колёс,
зубчатых реек, червяков. Резьбонарезной инструмент служит для получения и
обработки наружных и внутренних резьб. Номенклатуру резьбонарезного инструмента
составляют также резьбовые резцы и фрезы, метчики, плашки и др. К
абразивному инструменту относятся шлифовальные круги, бруски, хонинговальные
головки, наждачные полотна и др., применяемые для шлифования, полирования,
доводки деталей, а также для заточки инструмента. Алмазный инструмент
составляют круги, резцы фрезы с алмазными пластинами и др. (см. Инструмент
алмазный).
Станочный металлорежущий инструмент: 1 - резец с механическим креплением
пластинки твёрдого сплава; 2 - винтовое сверло; 3 - зенкер с коническим
хвостовиком, оснащённый твердосплавными пластинками; 4 - торцевая насадная
фреза со вставными ножами, оснащёнными твёрдым сплавом; 5 -машинная развёртка с
твердосплавными пластинками; 6 - плашка; 7 - винторезная головка с
круглыми гребёнками; 8 - червячная фреза; 9 -шлицевал протяжка; 10
-резцовая головка для обработки конических колёс с круговым зубом; 11 -
метчик; 12 - зуборезный долбяк со спиральными зубьями.
К ручным инструментам относятся зубила, напильники, надфили, ножовки,
шаберы и др., используемые без применения металлорежущего оборудования. Получили
распространение ручные машины с электрич., гидравлич. и пневматич.
приводом, рабочим органом к-рых являются ручные инструменты.
Форма и углы заточки режущей части М. и. (см. Геометрия резца), от
которых зависят его стойкость, производительность, экономичность, качество
обработки, выбираются с учётом свойств обрабатываемого материала,
смазывающе-охлаждающей жидкости, жёсткости системы станок - приспособление -
инструмент -деталь и т. д. Режущая способность М. и. определяется свойствами
материала, из к-рого изготовлена его режущая часть. Наиболее существенным
показателем является красностойкость материала. Применяют следующие осн.
группы материалов: инструментальные стали (углеродистые, быстрорежущие,
легированные), твёрдые сплавы, минерало-керамич. сверхтвёрдые материалы.
Инструмент из углеродистых сталей (красностойкость 200-250 °С) используют для
обработки обычных материалов при небольших скоростях резания. Быстрорежущие
стали, легированные вольфрамом, позволяют увеличить скорость резания в 2-4 раза.
Для обработки заготовок из жаропрочных сплавов и сталей повышенной прочности
применяют инструмент из стали с увеличенным содержанием ванадия, кобальта,
молибдена и пониженным содержанием вольфрама. Красностойкость этих сталей
достигает 600-620 °С, но одновременно возрастает их хрупкость. Твёрдые сплавы -
наиболее прогрессивные и распространённые материалы для М. и., вытесняющие
инструментальные стали (кроме случаев прерывистого точения и фасонного
фрезерования с большой глубиной), обладают красностойкостью 750-900 °С и высокой
износостойкостью. Твёрдые сплавы для М. и. выпускаются в виде пластинок
различной формы и размеров. Изготовляют также монолитные твердосплавные М. и.
небольших размеров. Ещё более высокими красностойкостью (1100-1200 °С) и
износостойкостью обладают М. и. с режущей частью, армированной минералокерамич.
пластинками, изготовленными на основе окиси алюминия с добавлением молибдена и
хрома. Однако применение минералокерамики ограничивается её низкой
пластичностью и большой хрупкостью. Перспективным является применение
сверхтвёрдых материалов - естественных и синтетических алмазов, кубического
нитрида бора и др. (для шлифования и затачивания М. и.).
Технологич. параметры М. и. зависят от глубины резания, подачи, скорости
резания (см. Обработка металлов резанием). Критерием износа режущей
части М. и. принято считать ширину изношенной площадки на задней поверхности
инструмента с учётом вида инструмента требуемой точности обработки и класса
чистоты. Стойкость М. и. определяется продолжительностью (в мин) непосредственного
резания между переточками. Гл. требование к М. и.- высокая производительность
при заданных классах чистоты и точности обработки - обеспечивается выполнением
условий в отношении допусков на изготовление, отклонений геометрич. параметров,
твёрдости режущей части, внеш. вида и т. д. Конструкция М. и. должна
предусматривать возможность многократных переточек, надёжное и быстрое
крепление. При проектировании металлорежущего оборудования учитываются спец.
элементы для крепления М. и.: резцедержатели, конусные отверстия, оправки и т.
п.
При создании новых конструкций М. и. стремятся усовершенствовать их
геометрич. параметры и конструктивные элементы, а также использовать материалы
с повышенными режущими свойствами и новые материалы. Решение этих проблем
позволяет повысить стойкость М. и. (в т. ч. размерную), улучшить дробление
стружки, в частности для автома-тич. линий и станков с программным управлением.
Важное значение имеют исследования физич. закономерностей изнашивания
инструмента, его геометрич. параметров, изыскание новых смазочно-охлаждающих
жидкостей. С вопросами произ-ва М. и. тесно связано создание новых конструкций
станков, внедрение современных электрохимических и электрофизических методов
для обработки твердосплавного инструмента. См. также Инструментальная
промышленность.
Лит.: Грановский Г. И., Металлорежущий инструмент, 2 изд., М., 1954;
Четвериков С. С., Металлорежущие инструменты, 5 изд., М., 1965; Ж и г а л к о
Н. И., Киселёв В. В., Проектирование и производство режущих инструментов,
Минск, 1969; Справочник технолога-машиностроителя, 3 изд., т. 1 - 2, М., 1972.
МЕТАЛЛОРЕЖУЩИЙ СТАНОК, машина для обработки резанием металлических и
др. материалов, полуфабрикатов или заготовок с целью получения из них изделий
путём снятия стружки металлорежущим инструментом.
М. с. являются осн. видом оборудования в машиностроении, приборостроении и
др. отраслях пром-сти. Совершенствование М. с. предопределяет
научно-технический прогресс, развитие технологии и организации
машиностроительного произ-ва.
Историческая справка. Обработка материалов резанием известна с
древних времён: деталь вращали вручную, обработка велась кремнёвым резцом. В 12
в. появились токарные и сверлильные станки с ручным приводом, а в 14 в.- с
приводом от водяных мельниц. Механич. станки для токарных работ изготовлялись
гл. обр. в Италии, Франции, откуда были завезены в Россию. Медальерными
станками славились петерб. мастера. В 1711 в Россию из Флоренции привезли
станок, сделанный мастером Зингером, приглашённым на службу Петром I. В
придворной токарне были изготовлены станки, в разработке конструкций и создании
к-рых принимал участие А. К. Нартов. Позднее Нартов построил другие
станки (гравёрные, копировальные, гильотинные), ему же принадлежит создание
первого в мире токарно-винторезного станка с механическим суппортом и сменными
зубчатыми колёсами (1738). Основные промышленные типы М. с. разрабатывались
позднее (Г. Модели и др.) в Великобритании, первой вступившей на путь
капиталистич. развития. В дальнейшем конструкция их совершенствовалась в
Германии, Франции, Швейцарии (точное станкостроение), позже (во 2-й пол. 19 в.)
в США (в частности, автоматич. станки для массового произ-ва). В России в
1712-14 на Тульском оружейном з-де мастер Я. Батищев создал прототип совр. агрегатных
станков для одноврем. сверления 24 ружейных стволов, в 1714 В. И. Геннин
построил на Олонецких з-дах многопозиционный станок. Значит, вклад в развитие
конструкции М. с. внёс М. В. Ломоносов, к-рый в сер. 18 в. построил и
применил в своих мастерских оригинальные шлифовальные и др. станки. Вклад в
создание новых конструкций станков внесли также рус. инженеры и изобретатели И.
Осипов, М. Сидоров, И. Ползунов, И. Кулибин, П. Захаво (первые
автоматы для нарезания резьбы, 1810), В. Игнатов, Г. Горохов. Но несмотря на
отд. выдающиеся изобретения, станкостроение в царской России развивалось
медленно. Только после Великой Окт. социалистич. революции в процессе
индустриализации маш.-строит. предприятия стали получать новые станки. В 1932
з-д "Красный пролетарий" выпустил первый соврем, токарно-винторезный
станок. В 1933 основан Экспериментальный н.-и. ин-т металлорежущих станков
(ЭНИМС), где было начато проектирование новых типов станков, изготовление гамм
станков токарных, револьверных, сверлильных, фрезерных и др. К 1970 в СССР
освоено 1817 типоразмеров М. с. Годовой выпуск составил 230 тыс. станков.
Большая заслуга в развитии станкостроения в СССР принадлежит сов. учёным В.
И. Дикушину, Н. С. Ачеркану, Д. Н. Решетову, А. П. Владзиевскому, Б. С. Балакшину,
Г. М. Головину, Г. А. Шаумяну, В. С. Васильеву, А. С. Проникову, В. А.
Кудинову, А. С. Брит-кину, Б. Л. Богуславскому, конструкторам Н. А. Волчеку, В.
Н. Кедринскому, И. А. Ростовцеву, Ю. Б. Эрпшеру и др.
Совершенствование произ-ва М. с. идёт в неск. направлениях. Намечается
увеличение выпуска агрегатных автоматич. и полуавтоматич. М. с. и автоматич.
линий, обеспечивающих автоматизацию тех-нологич. процессов в крупносерийном и
массовом произ-ве (в СССР выпуск таких М. с. за период 1966-70 увеличился на
22,6% при общем росте выпуска М. с. за этот период на 12%). В 1973 выпущено 211
тыс. М. с. Перспективно освоение прецизионных станков, обусловливающих
высокую точность и качество обработки деталей. Предусматривается дальнейшее
расширение произ-ва М. с. с числовым программным управлением (ЧПУ) для
обеспечения автоматизации механич. обработки изделий в индивидуальном и
серийном произ-ве. В 1968-70 в серийном произ-ве освоено 23 типоразмера таких
станков, в 1970-15 типов опытных образцов; их выпуск в 1973 составил 3800 шт.
Внедрение М. с. с использованием адаптивных систем управления (см. Самоприспосабливающаяся
система) открывает новые пути повышения точности обработки и
производительности. Для удовлетворения разнообразных потребностей нар. х-ва
намечается увеличение числа типов тяжёлых уникальных станков. К 1970 создано
ок. 500 типов тяжёлых уникальных М. с.
Классификация М. с. По специализации различают М. с. универсальные
для выполнения разнообразных операций на изделиях широкой номенклатуры; широкого
назначения для выполнения ограниченного числа операций на изделиях широкой
номенклатуры; специализированные для обработки однотипных изделий разных
размеров; специальныe для обработки изделий одного типоразмера; агрегатные
-специальные, состоящие из нормализованных деталей, узлов, силовых головок.
М. с. могут быть с ручным управлением (загрузка и установка заготовок, пуск,
переключение режима обработки, холостые движения, снятие изделия -вручную), а
также иметь различную степень автоматизации: полуавтоматы (установка заготовок,
пуск, снятие изделия -вручную, остальные движения цикла обработки -
автоматически), автоматы (все рабочие и холостые движения производятся
автоматически, человек осуществляет контроль за циклом работы); могут
составлять автоматические линии (группа автоматов, объединённая системой
транспортировки заготовок от одного к другому); иметь числовое программное
управление (все рабочие и холостые движения обеспечиваются заранее
закодированной программой, введённой в М. с. и посылающей преобразованные
импульсы на исполнительные и управляющие механизмы).
По точности различают 5 классов М. с.: Н-нормальной точности (напр.,
большинство универсальных М. с.), П -повышенной точности (на базе Н), В
-высокой точности, А - особо высокой точности (прецизионные), С - особо точные,
или мастер-станки.
По массе М. с. бывают лёгкие (до 1
т), средние (до 10 т), тяжёлые
(св. 10 т), уникальные (св. 100 т).
В зависимости от характера выполняемых работ и применяемого режущего
инструмента в СССР принята единая система классификации и условного обозначения
М. с. (табл.), разработанная в ЭНИМС. Все М. с. делятся на группы, к-рые, в
свою очередь, разбиваются на типы. По этой классификации каждому М. с.
серийного произ-ва присваивается шифр (индекс), к-рый образуется, как правило,
числом из 3 или 4 цифр; первая цифра указывает группу, вторая - тип, третья и
четвёртая характеризуют важнейшие размеры М. с. или обрабатываемого на нём
изделия. Напр., шифр 2150 обозначает вертикально-сверлильный станок с макс,
диаметром сверления 50 мм. После модернизации М. с.
Классификация металлорежущих станков.
|
Наименование группы станков
|
|
|
|
|
|
|
|
|
|
|
|
|
|
|
|
|
|
|
|
|
|
|
|
|
|
|
|
Токарно-винторез-ные и лобовые
|
|
Специализи-рованные для фасонных изделий
|
|
|
|
|
|
|
|
|
|
|
|
|
|
|
|
|
|
|
|
|
Горизонтально-сверлильные
|
|
|
Шлифовальные и доводочные
|
|
|
|
Специализированные шлифовальные
|
|
|
|
Притирочные и полировальные
|
Разные станки, работающие абразивом
|
|
|
|
|
|
|
|
|
|
|
|
|
Зубо- и резьбо- обрабатывающие
|
Зубострогальные для цилиндрических колёс
|
Зуборезные для кониче-ских колёс
|
Зубофрезерные для цилиндрических колёс и шлицевых валов
|
Зубофрезерные для червячных колёс
|
Для обработки торцов зубьев колёс
|
|
|
Зубо- и резьбо-шлифовальные
|
Разные зубо- и резьбообраба-тывающие
|
|
|
Вертикально-фрезерные консольные
|
Фрезерные непрерывного действия
|
|
Копировальные и гравировальные
|
вертикальные бесконсольные
|
|
|
Горизонтальные консольные
|
|
|
|
|
|
|
|
|
|
|
|
|
|
Строгальные, долбёжные и протяжные
|
|
|
|
|
|
|
|
|
|
|
|
|
|
|
|
|
|
|
|
|
работающие токарным резцом
|
работающие абразивным кругом
|
работающие гладким или на-сечённым диском
|
|
|
|
|
|
|
|
|
Муфто- и трубообра-батывающие
|
|
Правильно- и бесцентрово-обдирочные
|
|
Для испыта-ния инстру-мента
|
|
|
|
|
в его шифр за первой цифрой добавляется к.-л. буква. Напр., шифр 1К62
обозначает модернизированный токарно-винторезный станок с высотой центров 200 мм.
Модификация (видоизменение) базовой модели обозначается введением к.-л.
буквы в конце шифра. Напр., 6Н12К обозначает модификацию модернизированного
консольного вертикально-фрезерного станка. Описание типов станков см. в
статьях: Зубообрабатывающий станок, Карусельный станок, Токарный станок,
Сверлильный станок. Фрезерный станок, Шлифовальный станок.
Кинематика М. с. При обработке на М. с. очертания, форма деталей
(производящие линии) образуется в результате согласованных между собой
вращательных и прямолинейных движений заготовки и режущей кромки
металлорежущего инструмента. Эти движения, называемые рабочими, могут быть
простыми и сложными. В М. с. используются 4 метода получения производящих
линий: копирование, огибание (обкатка), методы следа и касания. При копировании
форма режущей кромки инструмента совпадает с формой производящей линии (рис. 1,
а, б); при огибании производящая линия возникает в форме огибающей ряда
последоват. положений режущей кромки инструмента, движущегося относительно
заготовки (рис. 1, в); при методе следа производящая линия образуется как след
движения точки режущей кромки инструмента (рис. 1, г, д); при методе
касания производящая линия является касательной к ряду геометрич. вспомогат.
линий, образованных реальной точкой (вершиной) движущейся режущей кромки
инструмента (рис. 1, е).
Рис. 1. Воспроизведения производящих линий методом: а, б - копирования;
в - огибания (обката); г, д - следа; е - касания; П -
производящая линия.
Рабочие движения в М. с.- главное движение и движение подачи. Главное
движение, происходящее в направлении вектора скорости резания, обеспечивает
отделение стружки от заготовки, а движение подачи - последовательное внедрение
инструмента в заготовку, "захват" новых, ещё не обработанных
участков. Главное движение в зависимости от типа М. с. может совершаться как
заготовкой (токарные, продольно-строгальные и др. станки), так и инструментом
(сверлильные, поперечно-строгальные, долбёжные, протяжные, фрезерные,
шлифовальные и др. станки); это движение может быть вращательным (токарные,
сверлильные, фрезерные, шлифовальные и др. М. с.) или поступательным
(строгальные, долбёжные, протяжные и др. М. с.). Помимо рабочих движений, на М.
с. совершаются также установочные и делительные движения, к-рые не используются
в процессе обработки резанием, однако необходимы для осуществления полного
технологич.
цикла. Все движения в М. с. обеспечивают соответствующие механизмы, в к-рые
входят различные передачи: ремённые, зубчатые, червячные, реечные, винтовые,
кулачковые, фрикционные и др. Эти передачи сочленяются между собой в
определённой последовательности и образуют кинематич. цепи, совокупность к-рых
составляет кинематич. схему М. с. При этом пользуются условными обозначениями
элементов и механизмов М. с. по ГОСТ 3462-61. На кинематич. схемах указываются
диаметры шкивов (Di, D2 и т. д.), числа зубьев зубчатых и червячных
колёс (zi, Zi и т. д.), шаги винтов, заходности червяков и винтов,
модули (т) нек-рых зубчатых колёс (обычно находящихся в зацеплении с
рейками), передаточные отношения плеч рычагов, характеристики звеньев настройки
и др.
Для станков с вращательным главным рабочим движением скорость резания
определяется по формуле:
V=пDn/1000 м/мин,
где D - макс, диаметр обработки (или макс, диаметр
инструмента) в мм; п -число оборотов шпинделя в минуту. Для конкретного
М. с. диаметр заготовки (инструмента) может быть различным, может производиться
также обработка заготовок из различных материалов и режущими инструментами с
режущей частью из разных инструмент, материалов (что приводит к выбору
соответствующих допускаемых скоростей резания). Привод главного движения должен
обеспечивать поэтому регулирование числа оборотов шпинделя. Существует
бесступенчатое и ступенчатое регулирование. В первом случае в определённом
интервале можно за счёт фрикционного, гидравлич. или электрич. привода
получить любое значение п. Во втором случае имеется определённый
конечный ряд различных п. Это обеспечивается за счёт использования коробок
скоростей с переключающимися зубчатыми колёсами. Для такого ряда рус.
учёным А. В. Га-долиным в 1876 разработана и обоснована теория построения рядов
чисел оборотов по закону геометрич. прогрессии. При такой закономерности потери
в устанавливаемых скоростях резания будут минимальными, а эксплуатационные
свойства станка наилучшими. По этому закону все числа оборотов шпинделя станка
в минуту от начального (миним.) n1 = n min до
конечного (макс.)nz = nмакс образуют геометрич. ряд, в
к-ром знаменатель геометрич. прогрессии ср определяется по формуле:
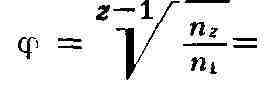
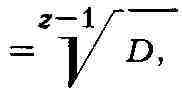
где D - диапазон регулирования числа оборотов шпинделя в 1 мин, z - количество
ступеней регулирования. В станкостроении СССР значения <р и соответствующие
им перепады скоростей А стандартизированы:
Примечание. Во втором ряду указаны допускаемые округления.
Осн. показатель любой кинематич. цепи - общее передаточное отношение: Uобщ=пк/пн=U1*U2*U3
..., где пк и пн - числа оборотов
соответственно конечного и начального звеньев в об/мин; U1, U2, U3 -
передаточные отношения отд. пар кинематич. цепи. Значение общ позволяет
определить значения конечных перемещений звеньев, связанных кинематич. цепью,
т. е. за готовки и режущего инструмента. Соответствующие функциональные связи
наз. уравнениями кинематич. баланса. Эти уравнения в 20-30-е гг. 20 в. выведены
сов. учёным Г. М. Головиным, предложившим единые формулы настройки для всех
станков.
Для вращающихся конечных звеньев уравнение кинематич. баланса: пк
= пн-U0бщ Для вращающегося начального звена и
поступательно-движущегося конечного: пн-Uобщ*Н = sммм/мин,
1об*Uобщ*Н = s мм/об, где Н - величина хода кинематич.
пары, преобразующей вращательное движение в прямолинейное, равная перемещению
прямолинейно-движущегося звена за один оборот вращающегося звена (для
токарного, сверлильного, фрезерного и др. станков).
Для М. с. с прямолинейным главным движением (строгальный, долбёжный,
протяжный и др.) различаются рабочий ход, в течение к-рого происходит резание,
и холостой (обратный) ход, в течение к-рого движущиеся части станка
возвращаются в исходное положение. Скорость холостого хода Vk = Vp- X,
где Vp -скорость рабочего хода; X = 1,5-- 2,5 - коэфф., выбираемый в
зависимости от типоразмера станка.
Рабочий и холостой ходы составляют двойной ход. Время двойного хода:
T=L/1000Up * (X+1)/X где L - длина хода (в мм). Число двойных
ходов (в 1 мин): п =1/T
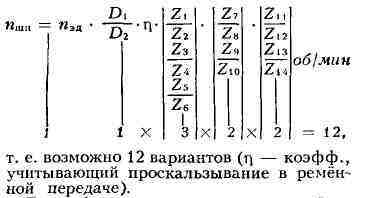
Рис. 2. Кинематическая схема главного привода токарного станка.
Рис. 3. Основные типы металлорежущих станков: 1 - универсальный
консольно-фрезерный станок (6Т82); 2 - вертикально-фрезерный станок с
копировальным устройством (6Н12К); 3 - токарный восьмишпиндельный
автомат (1К282); 4 - универсальный токарно-винторезный станок с
автоматическим циклом (1К62А); 5 - токарно-карусельный одностоечный станок с
числовым программным управлением (1512Ф2); 6 - вертикально-протяжной
станок (7Б705); 7 - копировальный поперечно-строгальный станок (ГД-21);
8 -
вертикально-сверлильный станок (2А135); 9 - радиально-сверлильный станок
(2А53); 10 - координатно-расточный станок (2В440); 11
- круглошлифовальный автомат (ЗК161); 12 - внутришлифовальный станок
(3260); 13 - станок для перешлифовки шатунных и коренных шеек коленчатых
валов (ЗА423); 14 - хонинговальный вертикальный одношпиндельный станок
(ЗБ833); 15 - зубодолбёжный полуавтомат (5122); 16 -
зубофрезерный станок (5К328А); 17 - зубострогальный полуавтомат
(5А250П); 18 - зубошлифовальный станок
Для облегчения кинематич. расчётов коробок скоростей применяется
графо-аналитич. метод. Зависимость чисел оборотов и передаточных отношений
изображается в виде графиков и структурных сеток.
Конструктивные особенности М. с.
Все кинематич. цепи и рабочие органы М. с. выполняются в виде конструктивных
узлов (механизмов), состоящих из различных деталей. Узлы и детали М. с. можно
разделить на 2 группы. Группа несущей и направляющей системы обеспечивает
правильное направление прямолинейных и круговых перемещений узлов с изделиями и
с режущими инструментами. К ней относятся станины и основания; детали и узлы
для поддержания и обеспечения прямолинейных перемещений изделий (консоли,
салазки столов, столы); детали и узлы для поддержания и обеспечения
прямолинейных и качательных перемещений режущих инструментов (суппорты, салазки
и поперечины суппортов, револьверные головки); детали и узлы для обеспечения
вращения изделий и режущих инструментов (шпиндели, опоры шпинделей, планшайбы,
вращающиеся колонны, задние бабки); детали и узлы для поддержания и направления
вращающихся деталей М. с. (корпуса коробок скоростей, коробок подач и
шпиндельных бабок). Группа привода и управления осуществляет формообразование
деталей и движения управления. К ней относятся механизмы гл. движения, движения
подачи и делительных движений; механизмы вспомогат. движений (транспортирующих,
зажимных, установочных, стружкоотводящих); механизмы управления (пуском и
остановом, скоростью и реверсированием равномерных движений), копировальные,
программные, адаптивные, самоподстраивающиеся системы. Конструктивные
компоновки М. с. различных типов могут быть самыми различными в соответствии с
рассмотренной ранее классификацией (рис. 3).
В развитии конструкций узлов М. с. существуют следующие тенденции:
оптимальное использование возможностей механич., электрич. и гидравлич.
приводов и их сочетаний; разработка прецизионных узлов и механизмов; уменьшение
трения в узлах станков; применение средств управления и автоматизации;
обеспечение высокой статич. и динамич. жёсткости; повышение долговечности за
счёт выбора оптимальных материалов и методов упрочнения деталей; применение
унификации, нормализации, стандартизации и агрегатирования.
Надёжность М. с. Надёжность М. с.-его свойство выполнять заданные
функции, т. е. обрабатывать изделия с сохранением в необходимых пределах
эксплуатационных показателей, гл. обр. точности и производительности, в течение
требуемого промежутка времени (наработки). Надёжность М. с. определяется
его безотказностью, долговечностью, ремонтопригодностью и
сохраняемостью.
На надёжность М. с. прежде всего влияют режимы и методы обработки, к-рые
предопределяют точность и качество обработанных поверхностей, а следовательно,
эксплуатационные характеристики изделий. Повышение надёжности М. с.
обеспечивается увеличением точности изготовления М. с.; созданием спец.
устройств для повышения точности обработки; применением систем автоматич.
регулирования для восстановления точности, снижающейся от действия процессов,
протекающих с различной скоростью, т. е. создание М. с. с автоматич.
подналадкой режимов обработки. Системы автоматич. регулирования -наиболее совр.
способ создания М. с. с высокой надёжностью. Автоматич. регулирование может
быть простым по заданной программе; прямым с учётом факторов, вызывающих
отклонение от программы; по замкнутому циклу с обратной связью. Последний
способ приводит к созданию адаптивных саморегулирующихся (самоподстраивающихся)
систем, дающих наибольшую надёжность М. с. Адаптивные системы управления М. с.
разделяются на следующие группы: стабилизирующие контролируемые параметры
резания; самоизменяющие управляющую программу; компенсирующие динамические и
температурные деформации системы СПИД (станок - приспособление - инструмент -
деталь); оптимизирующие режимы обработки по точности и производительности.
Использование адаптивных систем управления М. с. обеспечивает снижение (и даже
исключение) отказов из-за перегрузок, уменьшение зависимости результата
обработки от рабочего, упрощение программирования обработки, автоматич.
контроль получаемых размеров деталей, повышение экономичности обработки,
облегчение освоения новых методов обработки.
М. с. с числовым программным управлением. Числовое программное
управление (ЧПУ) М. с. экономически выгодно в серийном произ-ве, где происходит
сравнительно частая смена обрабатываемых изделий, а также при произ-ве
крупногабаритных деталей и деталей с криволинейными профилями и поверхностями.
ЧПУ позволяет автоматизировать процессы подготовки произ-ва и обработки, быстро
производить переналадку станка. В М. с. с ЧПУ информация о необходимых
перемещениях режущих инструментов относительно заготовки сообщается механизмам
управления М. с. в виде закодированной программы, представляющей собой условную
систему числовых обозначений. Эта программа вводится в считывающее устройство
М. с., к-рое преобразует её в соответствующие командные импульсы (электрич.
сигналы), а они при помощи механизмов управления передаются на исполнит, органы
М. с. (суппорты, салазки, столы и т. п.). Все действия, выполняемые узлами М.
с. по сигналам системы ЧПУ, разделяются на две группы: включения и выключения
для изменения режимов резания, смены действующих режущих инструментов и т. п.;
перемещения исполнит, органов.
Системы ЧПУ, применяемые в М. с., классифицируются: по назначению -для
позиционного, ступенчатого и функционального управления; по числу потоков
информации - разомкнутые, замкнутые и самонастраивающиеся; по виду
программоносителя - внутренние (панели с переключателями, штеккерные и кнопочные
панели и др.) и внешние (перфорированные карты и ленты, магнитные ленты,
киноленты и др.); по принципу ограничения перемещений исполнит, органов -
импульсные, аналоговые, путевые, временные, на схемах совпадения; по физ.
принципу контроля перемещений исполнит, органов - с механич., оптич., электрич.
и смешанными измерит, устройствами. Применяется также цикловая система
программного управления, при к-рой программируются (полностью или частично)цикл
работы М. с., режимы обработки и смена инструмента.
Системы ЧПУ М. с. состоят обычно из следующих основных автоматич. элементов
(рис. 4): устройство для ввода программы - "читает" программу и
преобразовывает её в сигналы управления; промежуточная "память" -
"запоминает" и в течение необходимого времени хранит полученные
сигналы управления; сравнивающее устройство (узел активного контроля) - при
помощи системы обратной связи сопоставляет перемещения, заданные программой и
фактически реализованные М. с. (при обнаружении разницы вырабатывает дополнит,
сигнал для исправления ошибки); исполнит, механизм, к-рый реализует через
соответствующие приводы (гидроцилиндры, винтовые пары, шаговые двигатели и др.)
полученные сигналы управления в необходимые перемещения исполнит, органов М. с.
Рис. 4. Структурная схема цифрового программного управления металлорежущего
станка: 1 - устройство для ввода программы; 2 - промежуточная
"память"; 3 - сравнивающее устройство; 4 - исполнительный
механизм; 5 - узел обратной связи (активного контроля).
Лит.:
Машиностроение. Энциклопедический справочник, т. 9, М., 1949;
Шувалов Ю. А., Веденский В. А., Металлорежущие станки, 2 изд., М., 1959; 3агорский Ф. Н., Очерки по истории металлорежущих станков до середины XIX века,
М.- Л., 1960; Металлорежущие станки, под ред. Н. С. Ачеркана, т. 1 - 2, М.,
1965; Агурский М. С., Вульфсон И.А., Ратмиров В. А., Числовое программное
управление станками, М., 1966; Шаумян Г. А., Кузнецов М. М., Волчкевич Л.
И., Автоматизация производственных процессов, М., 1967; Резание конструкционных
материалов, режущие инструменты и станки, М., 1967; П р о н и к о в А. С., Расчёт
и конструирование металлорежущих станков, 2 изд., М., 1967; Кучер И. М.,
Металлорежущие станки, 2 изд., Л., 1969; Самоподнастраивающиеся станки, [Сб.
ст.], под ред. Б. С. Балакшина, 3 изд., М., 1970; Налчан А. Г. (сост.),
Металлорежущие станки, М., 1970; Металлорежущие станки, М., 1970; Р а т м и р о
в В. А., Сиротенко А. П., Г а е в-ский Ю. С., Самонастраивающиеся системы
управления станками, М., 1971; Технологическая надёжность станков, М., 1971;
Детали и механизмы металлорежущих станков, под ред. Д. Н. Решетова, т. 1 - 2.
М., 1972.
Д. Л. Юдин.
МЕТАЛЛОРЕЖУЩИХ СТАНКОВ ЭКСПЕРИМЕНТАЛЬНЫЙ ИНСТИТУТ научно-исследовательский
(ЭНИМ С), в ведении Мин-ва станкостроительной и инструментальной пром-сти СССР.
Создан в Москве в 1933 на базе Н.-и. ин-та станков и инструментов и Центр,
конструкторского бюро по станкостроению. ЭНИМС разрабатывает теоретич. основы
развития станкостроения, организует и проводит науч. исследования в области
создания совр. конструкций металлорежущих станков, изготовляет
экспериментальные и опытные образцы станков с последующим их испытанием и
отработкой для серийного произ-ва в станкостроит. пром-сти. Имеет два филиала -
Вильнюсский и Закавказский (в Ереване), опытный з-д "Станкоконструкция"
в Москве с филиалами в Вильнюсе и Ереване. В ЭНИМС есть аспирантура с очной и
заочной формами обучения, ему дано право приёма к защите докторских и
кандидатских диссертаций. Ин-т систематически выпускает науч. труды в виде
рефератов работ ЭНИМС и сборников статей аспирантов, руководящие и информац.
материалы, отраслевые нормали и др. Награждён орденом Трудового Красного
Знамени (1971).
МЕТАЛЛОСТРОЙ, посёлок гор. типа в Ленинградской обл. РСФСР.
Расположен на левобережье р. Невы. Ж.-д. станция (Ижоры) в 20 км от
Ленинграда. 14,5 тыс. жит. (1970). Ленинградские заводы: высокочастотных
установок и железобетонных изделий; опытное произ-во электрич. машин.
МЕТАЛЛОТЕРМИЯ (от металлы и греч. therme - теплота), процессы,
основанные на восстановлении металлов из их соединений (окислов, галлоидов и
др.) более активными металлами (алюминием, магнием, кремнием, условно
принимаемым за металл, и др.), протекающие с выделением теплоты. М. начала
применяться на рубеже 19-20 вв. Металлотермич. процессы классифицируют по
металлу-восстановителю: алюминотермический (см. Алюминотермия), магниетермический,
силикотермический (см. Силикотермия). Металлотермич. способы произ-ва
более дорогие, чем углевосстановительные (см. Карботермия), и
используются для получения безуглеродистых легирующих сплавов высокого качества
(лигатуры с редкими металлами, безуглеродистый феррохром и др.), титановой
губки и др. чистых (гл. обр. по углероду) металлов и сплавов.
Существует неск. разновидностей металлотермич. процесса. В непечной процесс
проводится в тех случаях, когда теплоты, выделяющейся во время протекания
восстановит, реакций, достаточно для получения продуктов реакции в жидком
состоянии и хорошего их разделения (1750-2300 °С); используется в
алюмийотермии. Электропечной процесс применяется, когда выделяющейся теплоты
недостаточно для расплавления и необходимого перегрева продуктов плавки -
недостающее тепло подводится посредством электррнагрева; процесс широко
распространён. Вакуумная М. позволяет выделять легкоиспаряющиеся металлы
(напр., магний) во время их восстановления в условиях вакуума (при 800-1400 °С)
или получать металлы с пониженным содержанием газов.
Лит.:
Металлургия титана, М., 1968; Рысс М. А., Производство
ферросплавов, М., 1968; Беляев А. И., Металлургия лёгких металлов, 6 изд., М.,
1970.
В. А. Боголюбов.
МЕТАЛЛОТКАЦКИЙ СТАНОК, автоматич. станок для изготовления тканых
Металлич. сеток из различных видов проволоки - стальной, из цветных металлов и
сплавов круглого, квадратного, прямоугольного и др. сечений. М.
с. - видоизменённый ткацкий станок с той же принципиальной схемой. Как и в
обычных процессах ткачества, непрерывно повторяющееся передвижение ремизных рам
с галевами и челнока создаёт переплетения основных и уточных проволок, образуя
металлич. сетку. М. с. подразделяются на 3 основные группы: для лёгких, средних
и тяжёлых, особо плотных сеток. Отношение площади проволоки к общей площади
сетки составляет соответственно до 25%, от 25 до 50% и от 50 до 75%. На М. с.
могут быть выполнены разнообразные виды переплетений, по характеру которых
различают тканые металлич. сетки гладкие с квадратными ячейками, саржевые с
квадратными ячейками, фильтровые и др.
МЕТАЛЛОТРОПИЗМ (от металлы и греч. tropos - поворот,
направление), способность растений и микроорганизмов реагировать на присутствие
того или иного металла ростом в сторону металла (положительный М.) или от него
(отрицательный М.). Положительный М. к железу открыт в 1892 фин. ботаником Ф.
Эльвингом у мукорового гриба Phycomyces nitens. Отрицательный М. к меди и положительный
к железу и алюминию у того же гриба обнаружил рус. ботаник А. Г. Генкель
(1905). Металлы, испускающие (под влиянием радиоактивности среды - воздуха,
почвы) незначит. вторичное излучение (напр., алюминий), вызывают положительный
М., металлы с интенсивным излучением (напр., медь) - отрицательный.
Отрицательное дистантное действие металлов на бактерии и проростки горчицы
установлено рус. микробиологами Г. А. Надсоном и Е. А. Штерн в 1937.
МЕТАЛЛОФИЗИКА, раздел физики, изучающий строение и свойства металлов.
Как и физика диэлектриков и полупроводников, М. является
составной частью физики твёрдого тела. Совр. М. представляет собой
синтез микроскопич. теории, объясняющей свойства металлов особенностями их
атомного строения, и теоретич. металловедения, использующего
макроскопич. методы термодинамики, механики сплошных сред и др. для
исследования строения и свойств реальных металлич. материалов. Широкое
использование металлов привело к тому, что их основные физ. и хим. свойства
были изучены ещё в 19 в. Однако природа этих свойств це могла быть понята без
развития представлений об атомном строении вещества.
Микроскопическая теория металлов начала развиваться в 20 в. В 1900 П.
пруде предложил модель металла, в к-рой электропроводность осуществлялась
потоком "электронного газа", заполняющего промежутки между атомами.
Полагая, что электронный газ находится в тепловом равновесии и что под
действием приложенного электрич. поля электроны -"дрейфуют",
сталкиваясь с атомами, Друде получил правильную величину электропроводности
металлов при комнатных темп-pax, а также объяснил связь электро-и
теплопроводностей (Видемана - Франца закон). X. Лоренц развил
идею Друде, применив к электронному газу кинетич. теорию газов. Однако
построенная на применении законов классич. механики и статистики строгая теория
Друде - Лоренца оказалась более уязвимой при сопоставлении с экспериментом, чем
её примитивный вариант. Помимо того, что её выводы не соответствовали
температурной зависимости электропроводности, она не могла объяснить, почему
электронный газ не влияет на теплоёмкость металлов (не наблюдалось
заметного отклонения теплоёмкости металлов от Дюлонга и Пти закона, справедливого
как для металлов, так и для неметаллов). Не находила объяснения также величина
парамагнитной восприимчивости металлов, значительно меньшая, чем предсказывала
теория, и её независимость от темп-ры.
В 1927-28 В. Паули и А. Зоммерфельд объяснили
"аномалии" парамагнитной восприимчивости и теплоёмкости тем, что доля
электронов, участвующих в переносе электрич. заряда и тепла и ответственных за
спиновый парамагнетизм, очень мала. Основная же часть электронного газа при
обычных темп-рах находится в вырожденном состоянии, при к-ром она не реагирует
на изменение темп-ры (см. Вырожденный газ). Эти работы легли в основу
совр. электронной теории металлов. В 1930 Л. Ландау показал, что диамагнетизм
металлов обусловлен орбитальным движением этих же электронов и составляет 4/з
спинового парамагнетизма. В магнитных полях и при низких температурах он может
проявляться в виде сложной периодической зависимости магнитного момента от
поля. Квантовые осцилляции магнитной восприимчивости и электросопротивления в
магнитном поле были затем обнаружены экспериментально (см. Де Хааза - ван Альфена
эффект).
В 1929-30 Ф. Блох и Л. Бриллюэн рассмотрели влияние периодич.
поля кристаллич. решётки на электронный газ. Это позволило объяснить, напр.,
длину свободного пробега электронов в металле, намного превышающую среднее
расстояние между атомами, и привело к созданию зонной теории твёрдых тел. Для
металла определяющим является наличие незаполненной энергетич. зоны, через
к-рую проходит Ферми поверхность. Теплопроводность, электропроводность и
мн. др. свойства металлов определяются электронами именно этой зоны
(электронами проводимости). Исследуя отклик металла на воздействие статических
и переменных электрич. и магнитных полей (квантовые осцилляции, гальваномагнитные
явления, магнитоакустич. эффект, циклотронный резонанс и др.),
находят для электронов закон дисперсии (зависимость энергии от импульса). В
совокупности с данными об энергетич. спектре электронов (получаемых, напр., из
эмиссионных рентгеновских спектров) это даёт достаточно полное представление об
электронах в металле.
Изучение самой решётки также важно, т. к. её особенности определяют такие
свойства металлов, как теплоёмкость и электропроводность. Методы электронографии,
рентгенографии и нейтронографии позволили расшифровать атомную и
магнитную структуры металлов, а также исследовать тепловые колебания
кристаллич. решётки. Резонансные методы (ЭПР, ЯМР, Мёссбауэра эффект) сделали
возможным изучение локальных внутрикристаллич. магнитных и электрич. полей в
металлах (см. Кристаллическое поле).
Применение к электронам в металле теории обменного взаимодействия (В.
Геизенберг, П. Дирак, 1927) позволило понять природу ферромагнетизма
и обнаружить новые магнитоупорядоченные состояния металла - антиферромагнетизм
(Л.
Неель, 1932) и ферримагнетизм. Исследование взаимодействия
электронов друг с другом и с решёткой позволило раскрыть природу сверхпроводимости
(Дж. Бардин, Л. Купер, Дж. Шриффер, 1957). Изучение
нормальных, сверхпроводящих и магнитоупорядоченных (ферро-, антиферро- и
ферримаг-нитных) металлов - три основных направления микроскопич. теории
металлов.
Теория дефектов. Дефекты в кристаллах влияют практически на
все свойства металлов. Влияние дефектов начали изучать в 40-е годы в связи с
изучением диффузии и пластин, деформации (см. Пластичность). Центральное
место в теории дефектов занимает представление о дислокациях, перемещение
к-рых объясняет пластич. деформации кристаллов. Эти представления появились в
работах ряда исследователей (Л. Прандтль, 1928, Ю. Делингер, 1929, Е.
Орован, М. Поляни, У.Тейлор, 1934, Я. И. Френкель, 1938) вследствие
невозможности объяснить малое сопротивление деформации в рамках микроскопич.
теории идеального кристалла, дававшей оценку, в десятки тыс. раз
превосходящую наблюдаемые величины. Исследования дислокаций (в т. ч. с помощью
электронного микроскопа и рентгеновской топографии) в сочетании с теоретич.
исследованиями в 50-60-е гг. позволили объяснить большинство механич. свойств
металлов. Напр., предел текучести и деформационное старение металлов
объясняются упругим взаимодействием дислокаций с примесными атомами;
деформационное упрочение-дислокационными скоплениями (Н. Ф. Мотт, Ж. Фридель,
А. Зегер и др.); процессы полигонизации (разбиения деформированных
монокристаллов на блоки)- дислокационной структурой границ зёрен (В. Рид, У.
Шокли, Ф. Франк и др.).
Рождение и перемещение точечных дефектов приводят к образованию дислокации
и, кроме того, играют самостоят, роль в процессах диффузии, самодиффузии и
связанных с ними явлениях. Т. о., совокупность дефектов в кристалле, образующая
его дефектную структуру, определяет многие свойства реального металла. Это
относится не только к механическим свойствам. Рассеяние электронов и фононов
на дефектах может играть важную роль во мн. кинетич. явлениях в металлах.
Изучение влияния дефектов на физ. свойства - быстро развивающаяся область совр.
М.
Сплавы. Гетерофазные структуры. Способность образовывать твёрдые
растворы и сплавы - одно из важнейших свойств металлов, обеспечивающее им
широкое применение. Теория сплавов - старейшее направление М., развитие
к-poro тесно связано с проблемами практич. металловедения.
Явление полиморфизма широко используется на практике для придания
металлич. материалам желательных свойств путём термин, обработки. Полиморфное
превращение приводит к коренному изменению всех физ. свойств металла (нередко
при этом происходит превращение металла в неметалл). Важное направление в М. -
изучение полиморфных модификаций, возникающих в условиях высоких давлений,
сверхсильных магнитных полей и т. п. Исследование областей устойчивости
различных полиморфных фаз в зависимости от внешних условий (темп-ры, давления,
полей), а для сплавов также от концентрации позволяет построить диаграммы
состояния.
Теория фаз, начавшая развиваться ещё в 19 в., рассматривает фазовые
равновесия, фазовые превращения, а также структуру и свойства гетерофазных
систем. Превращение одной фазы в другую, как правило, происходит путём
образования в исходной фазе отд. кристаллов новой фазы, к-рые растут,
взаимодействуют и образуют сложную гетерофазную систему (см. Двойные системы). Форма, размер и взаимное расположение кристаллов определяют
гетерофазную структуру реального металла. Регулируя гетерофазиую структуру,
можно изменять свойства металлич. материалов. При этом свойства гетерофазной
системы могут не сводиться к "сумме свойств" отд. фаз. Такая
неаддитивность свойств связана с наличием межфазных границ, удельный объём
к-рых в мелкодисперсных системах может быть достаточно велик, а также со
значит, искажением фаз из-за их упругого взаимодействия. Влияние упругого
взаимодействия фаз наиболее полно проявляется при фазовых превращениях
мартенситного типа, когда не меняются ни состав, ни степень порядка, а фазы
отличаются только положением узлов кристаллич. решёток. Физ. природа мартенситных
превращений исследовалась в работах Г. В. Курдюмова с сотрудниками
(см. также Мартенсит).
Изучение эволюции гетерофазной системы во времени при различных внешних
условиях, т. е. кинетики фазового превращения, позволяет судить о промежуточных
состояниях гетерофазной структуры, к-рые возникают в процессе превращения и
затем могут достаточно долго сохраняться, если изменение внешних условий
"замораживает превращение. Примером такой неравновесной гетерофазной
структуры служат поликристаллы, размер зёрен к-рых определяется
скоростью зарождения и роста зёрен в процессе кристаллизации. Вследствие
упругого взаимодействия между фазами часто образуются многофазные
метаста-бильные состояния, характеризующиеся регулярным пространств,
расположением фаз.
Т. о., строение реальных металлов характеризуется наличием трёх структур
различного масштаба: микроскопической (атомно-кристаллической), дефектной и
гетерофазной. Между различными -"этажами" этой "иерархии"
структур существует тесная взаимосвязь, однако различие в масштабах оправдывает
исторически сложившееся различие в методах их эксперимент, и теоретич.
изучения. С этим связано существование трёх направлений М.: микроскопич. теория
металлов, исследования дефектов и их влияния на свойства металлов, изучение фаз
и гетерофазных металлич. материалов, к-рые с различных сторон решают общую
проблему М.- связь физических свойств металла и наблюдающихся в нём явлений с
его строением и зависимость внутреннего строения металлов от внешних условий.
Лит. см. при ст. Металлы.
Ю. А. Осипъян, А. Л. Ройтбурд.
МЕТАЛЛОФОНЫ (от металлы и греч. phone - звук), музыкальные
инструменты, источником звука которых служит их упругое металлич. тело. См. Тарелки,
Маримба, Тубофон, Колокола, Треугольник, Вибрафон, Гонг, Челеста.
МЕТАЛЛСОДЕРЖАЩЕЕ ТОПЛИВО, топливо для ракетного двигателя, содержащее
лёгкие металлы - Li, Be, Mg, А1 и др.- в виде порошка или их хим. соединений*
(гидриды, металлоорганич. соединения). Металлы и их соединения в ряде случаев
увеличивают удельную тягу; этим преимуществом обладают и борсодержащие
топлива. Применяются алюминизированные твёрдые ракетные топлива, а также жидкое
пусковое М. т. (триэтилалюминий) для обеспечения хим. зажигания в двигателях,
использующих жидкий кислород в качестве окислителя. Проводятся эксперимент,
работы по освоению бор- и бериллийсодержащих ракетных топлив.
"МЕТАЛЛУРГ", ежемесячный производств.-массовый журнал
Мин-ва чёрной металлургии СССР и ЦК профсоюза рабочих металлургич. пром-сти.
Выходит в Москве с 1956. Переиздаётся на англ. языке в США. Освещает вопросы
внедрения новой техники и передовой технологии, механизации и автоматизации произ-ва, модернизации оборудования и повышения производительности труда.
Публикует материалы о передовиках произ-ва чёрной металлургии, по экономике и
технике безопасности отрасли, о работе творч. объединений и др. Тираж (1974) 23
тыс. экз.
МЕТАЛЛУРГИИ ИНСТИТУТ им. А. А. Байкова Академии наук СССР, н.-и.
учреждение, ведущее работы по металлургии, металловедению и обработке чёрных,
цветных и редких металлов и сплавов. Создан в Москве в 1938. Изучает
физико-хим. основы процессов получения металлов и сплавов, в т. ч. новых
металлич. материалов со спец. свойствами; разрабатывает эффективные процессы
произ-ва и обработки металлов. Результаты работ публикуются в сборниках ин-та,
монографиях, "Докладах АН СССР", "Известиях Академии наук СССР.
Металлы", в журнале "Физика и химия обработки материалов" и др.
В М. и. имеется аспирантура (ин-ту дано право приёма к защите докторских и
кандидатских диссертаций), своё СКВ, разрабатывающее приборы и установки для
исследований в области металлургии. Организатором и первым директором ин-та был
акад. АН СССР И. П. Бардин; в ин-те работали академики АН СССР А. А. Банков, Э.
В. Брицке, Н. Т. Гудцов, М. М. Карнаухов, М. А. Павлов, А. М. Самарин,
чл.-корр. АН СССР И. А. Одинг и др.
МЕТАЛЛУРГИЧЕСКАЯ ПЕЧЬ, тепловой агрегат для выплавки металлов и
сплавов, нагрева слитков и заготовок перед прокаткой, термич. обработки
прокатной продукции и др. целей. См. Печь.
МЕТАЛЛУРГИЧЕСКОЕ МАШИНОСТРОЕНИЕ, см. в ст. Тяжёлое машиностроение.
МЕТАЛЛУРГИЧЕСКОЕ ОБРАЗОВАНИЕ, отрасль технического образования, имеющая
целью подготовку инженеров и техников различного профиля по выплавке чёрных и
цветных металлов и сплавов, по обработке их давлением, металловедению,
металлофизике, термич. обработке металлов, литейному произ-ву, экономике и
организации металлургич. произ-ва и др.
История и развитие М. о. тесно связаны с горным образованием. В
России в 18-19 вв. квалифицированные рабочие и мастера-металлурги готовились в
горнозаводских школах и горных уч-щах. Наиболее высокий уровень подготовки
(соответствующий квалификации техника) был достигнут в Уральском горном,
Пермском реальном (на горнопром. отделении), Нижнетагильском горнозаводском,
Домбровском горном уч-щах и в горном уч-ще Полякова в Горловке.
Высшее М. о. возникло в России во 2-й пол. 18 в., когда в 1773 в Петербурге
открылось Горное уч-ще, переименованное впоследствии в Горный ин-т. В течение
столетия Горный ин-т являлся единственным горно-металлургич. вузом России. Из
него вышли выдающиеся учёные, внёсшие большой вклад в развитие отечеств,
металлургии: П. П. Аносов, Н. А. Курнаков, М. А. Павлов и др. В 1834
преподавателями ин-та была организована в Петербурге Горная школа для
подготовки техников-металлургов (один из выпускников этой школы Д. К. Чернов
стал впоследствии основоположником металловедения).
Металлургич. знания впервые начали сообщаться в Петербургском горном ин-те в
курсе "Наставление учителю химического класса". В этом курсе металлургия
была составной частью химии; в 1804 курс металлургии стал самостоят,
дисциплиной. Позднее в Горном ин-те выделились как самостоятельные горное и
заводское отделения (на заводском отделении, к-рое давало высшее М. о.,
читались курсы физ. химии и металлургии). С развитием горнозаводской пром-сти
на юге России открылись новые спец. уч. заведения. В 1899 в Екатеринославе
(ныне Днепропетровск) основано Высшее горное уч-ще, в к-ром преподавалась
металлургия (в 1921 преобразовано в Горный ин-т им. Артёма, из которого в 1930
выделился Днепропетровский металлургический институт); в 1898 в Киеве
открылся поли-технич. ин-т, где готовились и инженеры-технологи по металлургии.
В нач. 20 в. созданы Томский технологич. (1900), Петерб. политехнич. (1902) и
Новочеркасский политехнич. (1907) ин-ты, где также осуществлялась подготовка
инженеров-металлургов. Известная науч. металлургич. школа сложилась в Петерб.
политехнич. ин-те, в к-ром преподавали виднейшие учёные-металлурги А. А.
Байков, Mi А. Павлов, В. Е. Грум-Гржимайло и др.
Бурное развитие металлургии и М. о. началось после Окт. революции 1917. В
1918 в Москве открылась Горная академия, в составе к-рой был и металлур-гич.
ф-т; в 1930 на базе ф-тов академии созданы Моск. ин-т стали (ныне Московский
институт стали и сплавов) и Моск. ин-т цветных металлов и золота (см. в ст.
Красноярский институт цветных металлов). В период индустриализации
страны для подготовки специалистов-металлургов организованы ме-таллургич. и
горно-металлургич. ин-ты: Сибирский (в Новокузнецке, 1930), Мариупольский (ныне
Ждановский, 1930), Московский вечерний (1931), Северокавказский (в
Орджоникидзе, 1931), Магнитогорский (1932) и др., а также неск. металлургич.
техникумов.
Строительство крупных металлургич. з-дов, оснащённых совр. техникой,
потребовало не только увеличения числа инженеров, но и улучшения их подготовки.
В 1937 были пересмотрены уч. планы металлургич. ин-тов и установлены 3 основные
специальности: металлургия чёрных металлов (доменное, сталеплавильное и
литейное произ-во); пластич. и термич. обработка металлов (прокатное произ-во,
ковка, штамповка и термич. обработка); механич. оборудование металлургич.
цехов. В уч. планы включены новые дисциплины: теория металлургич. процессов,
металлургич. печи, огнеупорные материалы, металлургия чугуна и стали, обработка
металлов давлением, рентгенография и испытание металлов, экономика металлургии,
техника безопасности и др.
Система совр. М. о. в СССР основана на органич. соединении теоретич.
обучения с практич. подготовкой будущих специалистов. Теоретич. фундамент М. о.
составляют физико-математич. и хим. науки, механика (теоретич. и прикладная),
металловедение, теория металлургич. процессов, электроника, экономика и др. Все
студенты изучают марксистско-ленинскую теорию. В уч. планы старших курсов
включены спец. дисциплины, определяющие специализацию в области металлургии.
В соответствии с требованиями научно-технич. революции и новыми задачами
коммунистич. строительства в вузах расширено изучение фундаментальных наук,
новых курсов: науч. организации труда, автоматизированных систем управления,
электронно-вычислит. машин и их практич. применения в металлургии, инженерной
психологии и др. Широкое привлечение студентов к участию в науч. исследованиях,
а также введение учебной н.-и. практики стали одними из основных методов
воспитания творческого специалиста.
Совр. М. о. имеет стройную систему специальностей и отражает состояние
металлургич. пром-сти и науки. В связи с потребностями нар. х-ва, науки и
техники введены новые специальности: физика металлов, физико-хим. исследования
металлургич. процессов, автоматизация и комплексная механизация металлургич.
пром-сти, произ-во чистых металлов и полупроводниковых материалов, кибернетика
металлургич. произ-ва, физ. методы пыле- и газоулавливания на металлургич.
предприятиях. Срок обучения в металлургич. вузах (ф-тах) -5-5,5 лет.
В 1973 подготовка инженеров-металлургов в СССР осуществлялась в металлургич.
и горно-металлургич. ин-тах Москвы, Днепропетровска, Жданова, Красноярска,
Магнитогорска, Орджоникидзе, Новокузнецка, в Коммунарском горно-металлургич.
ин-те (осн. в 1958 в Коммунарске Ворошиловградской обл.), а также в Ленингр.
горном ин-те, на металлургич. ф-тах Ленинградского, Уральского (Свердловск),
Челябинского, Иркутского, Киевского, Донецкого, Казахского (Алма-Ата),
Карагандинского, Грузинского (Тбилиси), Липецкого политехнич. ин-тов,
Днепродзержинского индустриального ин-та (в большинстве этих вузов имеются
дневные, вечерние и заочные отделения), Норильского и Краматорского вечерних
индустриальных ин-тов, Всесоюзного (Москва), Северо-Западного (Ленинград) и
Украинского (Харьков) заочных политехнич. ин-тов, на заводе-втузе при
Карагандинском металлургич. комбинате (Темиртау), в Московском вечернем
металлургическом ин-те.
Подготовка техников-металлургов осуществляется в СССР по широкой
номенклатуре специальностей в горно-металлургич. и металлургич. техникумах
Свердловска, Первоуральска, Серова, Москвы, Челябинска, Златоуста,
Днепродзержинска, Никополя, Днепропетровска, Кривого Рога, Енакиева, Макеевки,
Запорожья и др., а также в индустриальных техникумах Новокузнецка, Златоуста,
Днепропетровска и др. Срок обучения - 4 года (см. Среднее специальное
образование). В 1972/73 уч. г. на специальностях М. о. обучалось: в вузах
54,5 тыс. чел., в техникумах - 48,5 тыс. чел.; приём соответственно составил: в
вузах - 11,6 тыс. чел., в техникумах - 14,9 тыс. чел.; выпуск - 8 тыс. чел. и
11,2 тыс. чел. Пед. и науч. кадры в области металлургии готовятся в
аспирантуре, организованной в более чем 30 металлургич., горно-металлургич.,
политехнич., индустриальных втузах и н.-и. учреждениях. Моск. ин-ту стали и
сплавов, Днепропетровскому и Магнитогорскому им. Г. И. Носова металлургическим
ин-там предоставлено право принимать к защите докторские и кандидатские
диссертации, Моск. вечернему, Северокавказскому и Сибирскому им. Серго
Орджоникидзе ин-там - кандидатские. Квалифицированных рабочих для металлургич.
пром-сти (горновые доменных печей, подручные сталеваров, вальцовщики,
плавильщики и др.) выпускают профессионально-технические учебные заведения (см.
также Профессионально-техническое образование).
Существенный вклад в развитие металлургии и М. о. внесли известные сов.
учёные И. П. Бардин, Б. В. Старк, М. М. Карнаухов, А. Н. Вельский, А. М. Самарин,
В. П. Елютин, А. А. Бочвар и др.
В др. социалистич. странах подготовка металлургов осуществляется: в ГДР - во Фрейбергской горной академии, в Дрезденской высшей технич. школе; в Польше - в
Краковской горно-металлургич. академии, Варшавском и Познанском политехнич.
ин-тах; в Чехословакии - в Горно-металлургич. школе (Острава), в Высшей технич.
школе (Кошице); в Венгрии - в Будапештском политехническом ин-те; в
Болгарии - в Софийском химико-технологическом ин-те.
В капиталистич. странах М. о., как правило, осуществляется в инж. колледжах
или на металлургич. ф-тах, входящих в состав ун-тов. Важнейшими центрами М. о.
являются: в США - Массачусетсский технологич. ин-т (Кембридж), Технологич. ин-т
Карнеги (Питсбург), металлургич. ф-ты и колледжи Гарвардского, Нью-Йоркского,
Колумбийского, Чикагского и др. ун-тов; в Великобритании - металлургич. ф-ты и
колледжи ун-тов Кембриджа, Бирмингема, Манчестера, Лидса и Шеффилда; в ФРГ
-Горная академия в Клаустале, высшие технич. школы в Ахене, Кёльне, Гамбурге и
др.; во Франции - Центральные н.-и. ин-ты металлургии в Париже и Сент-Этьенне,
Высшая нац. школа электрохимии и электрометаллургии в Гренобле и др. В
развивающихся странах М. о. осуществляют: в Индии - Бомбейский, Кхарагпурский и
Канпурский технологич. ин-ты, Бенгальский инж. колледж, инж. колледжи в Пуне и
Варанаси; Бирме - Рангунский технологический ин-т; АРЕ - Каирский ун-т,
Эт-Таббинский металлургический ин-т; Алжире - Аннабский горно-металлургический
ин-т и др.
Лит.: Высшие учебные заведения горной и металлургической
промышленности СССР, М., 1948; Полухин П. И., О подготовке
специалистов-металлургов в США, "Вестник высшей школы", 1958, № 3; е
г о же, Новый этап в развитии советской высшей школы, М., 1960; его же, Высшее
металлургическое образование в СССР за 50 лет, "Известия вузов. Чёрная
металлургия", 1967, №10; Веселова А. Н., Среднее
профессионально-техническое образование в дореволюционной России, М., 1959. См.
также лит. при ст. Горное образование.
П. И. Полухин.
МЕТАЛЛУРГИЯ (от греч. metallurgeo - добываю руду, обрабатываю металлы
от metallon - рудник, металл и ergon - работа), в первоначальном, узком значении
- искусство извлечения металлов из руд; в совр. значении - область науки и
техники и отрасль пром-сти, охватывающие процессы получения металлов из руд или
др. материалов, а также процессы, связанные с изменением хим. состава,
структуры, а следовательно, и свойств металлич. сплавов. К М. относятся:
предварительная обработка добытых из недр земли руд, получение и рафинирование
металлов и сплавов; придание им определённой формы и свойств.
В совр. технике исторически сложилось разделение М. на чёрную и цветную. Чёрная
металлургия охватывает произ-во сплавов на основе железа: чугуна, стали,
ферросплавов (на долю чёрных металлов приходится ок. 95% всей производимой
в мире металлопродукции). Цветная металлургия включает производство
большинства остальных металлов (см. Металлы в технике). В связи с
использованием атомной энергии развивается произ-во радиоактивных металлов.
Металлургич. процессы применяются также для производства полупроводников и
неметаллов (кремний, германий, селен, теллур, мышьяк, фосфор, сера и др.);
нек-рые из них получают попутно с извлечением металлов. В целом совр. М.
охватывает процессы получения почти всех элементов периодической системы, за
исключением галоидов и газов.
Возникнойение М., как показывают археологич. находки, относится к глубокой
древности (см. рис. 1). Обнаруженные в 50-60-х гг. 20 в. в юго-зап. части М.
Азии следы выплавки меди датируются 7-6-м тыс. до н. э. Примерно в это же время
человек познакомился с самородными металлами: золотом, серебром, медью, а затем
и с метеоритным железом. Сначала металлические изделия изготовляли путём
обработки металлов в холодном состоянии. Медь и железо с трудом подвергались
такой обработке и поэтому не могли найти широкого применения. После изобретения
горячей кузнечной обработки (ковки) медные изделия получили более широкое
распространение (эпоха энеолита). Овладение искусством выплавки меди из
окисленных медных руд и придания ей нужной формы литьём (5-4 тыс. до н. э.)
привело к быстрому росту произ-ва меди и к значит, расширению её применения.
Однако ограниченное кол-во месторождений окисленных медных руд обусловило
необходимость освоения гораздо более сложного процесса переработки сульфидных
руд с применением предварит, обжига руды и рафинирования меди путём повторного
плавления. Возникновение этого процесса относится примерно к сер. 2-го тыс. до
н. э. (Бл. Восток, Центр. Европа).
Во 2-м тыс. до н. э. начали широко применяться изделия из б р о н з ы
(сплава меди с оловом), к-рые по качеству значительно превосходили медные.
Бронзовые орудия труда, оружие и др. предметы отличались большей устойчивостью
против коррозии, упругостью, твёрдостью, остротой лезвия. Кроме того, бронза
имела более низкую темп-ру плавления, чем медь, и лучше заполняла литейную
форму. Из неё легче было отливать всевозможные изделия. Вытеснение меди бронзой
означало переход к бронзовому веку. В кон. 3-го и во 2-м тыс. до н. э.
крупным центром М. меди и бронзы на территории СССР был Кавказ.
Рис. 1. Плавка металла в Древнем Египте (дутьё подаётся мехами, сшитыми из
шкур животных).
Примерно в сер. 2-го тыс. до н. э. человек начинает овладевать и искусством
получения железа из руд. Сначала для этой цели использовали костры, а затем
спец. плавильные ямы - сыродутные горны (см. Сыродутный процесс). В
горн, выложенный из камня, загружали легковосстановимую руду и древесный уголь.
Дутьё, необходимое для горения угля, подавалось в горн снизу (первое время
естеств. тягой, а впоследствии при помощи мехов). Образующиеся газы (окись
углерода) восстанавливали окислы железа. Относительно низкая темп-pa процесса и
большое кол-во железистого шлака препятствовали науглероживанию металла и
позволяли получать железо только с низким содержанием углерода. Процесс был
малопроизводительным и обеспечивал извлечение из руды лишь около половины
содержащегося в ней железа. М. железа развивалась очень медленно, несмотря на
то, что железные руды гораздо более распространены, чем медные, а темп-ра их
восстановления ниже. Причина первоочередного развития М. меди заключается в
том, что сыродутное железо по качеству значительно уступало меди. Это
объясняется прежде всего тем, что при достижимых в то время темп-pax процесса
медь получалась в расплавл. состоянии, а железо - в виде тестообразной массы с
многочисл. включениями шлака и несгоревшего древесного угля. В связи с низким
содержанием углерода сыродутное железо было мягким - изготовленные из него
оружие и орудия труда быстро затуплялись, гнулись, не подвергались закалке; они
уступали по качеству бронзовым. Для перехода к более широкому произ-ву и
применению железа необходимо было усовершенствовать примитивный сыродутный
процесс, а главное - овладеть процессами науглероживания железа и его последующей
закалки, т. е. получения стали. Эти усовершенствования обеспечили железу в 1-м
тыс. до н. э. главенствующее положение среди материалов, используемых человеком
(см. Железный век). К нач. н. э. М. железа была почти повсеместно
распространена в Европе и Азии.
На протяжении почти 3 тысячелетий М. железа не претерпела принципиальных
изменений. Постепенно процесс совершенствовался: увеличивались размеры
сыродутных горнов, улучшалась их форма, повышалась мощность дутья; в результате
горны превратились в небольшие печи для произ-ва сыродутного железа - домницы
(рис. 2). Дальнейшее увеличение размеров домниц привело в сер. 14 в. к
появлению небольших доменных печей (см. Доменное производство). Увеличение
высоты этих печей и более интенсивная подача дутья способствовали повышению
темп-ры и значительно более сильному развитию процессов восстановления и
науглероживания металла. Вместо тестообразной массы сыродутного железа в
доменных печах получали уже высокоуглеродистый железный расплав с примесями
кремния и марганца - чугун. Росту произ-ва чугуна способствовало изобретение в
14 в. способа передела его в ковкое железо - т. н. кричного передела. Переплавляя
чугун в кричном горне, его рафинировали от примесей путём окисления их
кислородом дутья и специально загружаемого в горн железистого шлака. Кричный
процесс постепенно вытеснил прежние малопроизводит. способы получения стали на
основе сыродутного железа, несмотря на достигнутое с их помощью чрезвычайно
высокое качество металла (см. Булат, Дамасская сталь). Т. о., возник двухстадийный
способ получения железа, сохранивший своё значение и являющийся основой совр.
схем произ-ва стали. След, этапом развития М. стали в Европе было появление в
Англии в 1740 тигельной плавки (задолго до того известной на Востоке) и
в последней четв. 18 в.- пудлингования. Тигельный процесс был первым
способом производства литой стали. Её выплавляли в тиглях из огнеупорной
глины, к-рые устанавливались в спец. печи. В пудлинговом процессе, как и в
кричном, получали т. н. сварочное железо. Для этого чугун рафинировали от
углерода и др. примесей на поду отражательной печи.
Рис. 2. Домница (штюкофен) в Германии 15-16 вв.
Несмотря на большое значение для развития техники своего времени, тигельный
и пудлинговый процессы не могли удовлетворить потребности в стали. М. чугуна
развивалась опережающими темпами. Этому способствовало внедрение водяных
воздуходувных труб (рис. 3), мехов с приводом от водяного колеса (с 15 в.),
паровых воздуходувных машин (1782). В кон. 18 в. в доменном произ-ве начали
широко использовать кам.-уг. кокс (1735); к 19 в. относится начало применения
нагретого дутья и тщательной подготовки руды к доменной плавке. Отставание
сталеплавильного произ-ва проявлялось в том, что кол-во выплавляемого чугуна
долгое время (до нач. 20 в.) превышало кол-во производимой стали. Гл. роль в
наступившем переломе сыграло изобретение трёх новых процессов произ-ва литой
стали: в 1856-бессемеровского процесса, в 1864 - мартеновского (см.
Мартеновское производство) и в 1878 - томасовского процесса. Распространение этих
процессов (в первую очередь мартеновского, к-рому свойственно использование
большого кол-ва металлич. лома) привело к тому, что к сер. 20 в. выпуск чугуна
составлял уже только 70% от выплавки стали.
Рис. 3. Каталонский горн с водяной воздуходувной трубой: 1 - клапан; 2
- отверстия для воздуха; 3 - труба; 4 - слив воды; 5 -дутьё; 6 - фурма;
7 - руда и древесный
уголь: 8 - крица; 9 - шлак; 10 - выпуск шлака.
Дальнейшее развитие сталеплавильного произ-ва во 2-й пол. 20 в. связано с существенным
увеличением ёмкости и производительности агрегатов, широким применением
кислорода для повышения эффективности металлургич. процессов, появлением
нового, быстро развивающегося способа получения стали в кислородных конвертерах
(см. Кислородно-конвертерный процесс), с развитием внепечного
рафинирования жидкой стали в вакууме, обработки стали синтетич. шлаками и
инертным газом, с внедрением непрерывной разливки стали, широкой
механизацией и автоматизацией производств, процессов. Большое значение в совр.
М. железа имеет выплавка высококачеств. и в т. ч. легированной стали, к-рая
с нач. 20 в. производится в основном в электропечах (см.
Электросталеплавильное производство). Со 2-й пол. 20 в. для получения нек-рых цветных металлов, а
также стали особо ответств. назначения начали применять дополнит, переплав
металла в дуговых вакуумных печах, электрошлаковых, электроннолучевых и
плазменных установках (см. Электрошлаковый переплав, Электроннолучевая
плавка, Плазменная металлургия). В области извлечения железа из руд наряду
с доменным произ-вом, к-рое продолжает расширяться, развиваются разнообразные
способы прямого получения железа. Этим процессам, позволяющим получать
железо, пригодное для выплавки стали в электропечах, принадлежит большое
будущее.
Кроме железа, в древнем мире добывали и применяли золото, серебро, медь,
олово, свинец, ртуть. Мн. др. металлы (в т. ч. неизвестные древним)
использовались в сплавах, минералах или соединениях.
Золото в виде песка и самородков добывали в доисторич. времена из россыпей
путём промывки. Для получения изделий золотой песок подвергали горячей ковке
(кузнечной сварке) или переплавляли в тиглях. При этом обычно получали сплавы
золота с серебром и др. элементами, что обусловливало разнообразные вариации
цвета, а также литейных и механич. свойств металла. Рафинирование золота
и отделение его от серебра началось во 2-й пол. 2-го тыс. до н. э., но до 6 в.
до н. э. распространялось довольно медленно. Удаление примесей (вместе со
свинцом, добавляемым для улучшения процесса) производили путём окисления их
воздухом. Отделение серебра осуществляли путём хлорирования сплава при нагреве
в присутствии поваренной соли, с последующей отгонкой летучих хлоридов или их
растворением. Др. способ отделения серебра заключался в переводе его в сульфиды
при нагревании сплава с сернистыми материалами и древесным углём. Применение
азотной кислоты для отделения серебра от золота относится уже к 13-14 вв.
Процесс амальгамации также был известен в древнем мире, но уверенности в
том, что он применялся для извлечения золота из руд и песков, нет. После
открытия рус. учёным П. Р. Багратионом в 1843 основ цианирования золотых
руд и особенно после работ англ, металлургов Дж. С. Мак-Артура и бр. Р. и У.
Форрестов (1887-88) этот процесс занял ведущее место в М. золота; иногда он
используется в соединении с амальгамацией. Успешно применяется для извлечения
золота флотационное (см. Флотация) и гравитационное обогащение.
Серебро в древности получали главным образом попутно со свинцом из галенита.
Начало их совместной выплавки можно отнести к 3-му тыс. до н. э. (М. Азия);
широкое распространение процесс получил только через 1500-2000 лет. Можно
полагать, что техноло-гич. схема включала в себя обжиг руды, горновую плавку,
разделительную плавку (ликвационное рафинирование, зейгерование) и купеляцию.
Во 2-й пол. 20 в. свинец получают преим. из полиметал-лич. руд в результате
флотационного обогащения, агломерирующего обжига, восстановит, плавки в шахтных
печах и рафинирования продукта этой плавки -чернового свинца (веркблея). При
рафинировании извлекается также серебро (и золото, если оно есть).
Массовое произ-во меди началось после изобретения В. А. Семенниковым в
1866 конвертирования штейна. Большую роль в развитии конвертерной
переработки штейна сыграла предложенная в 1880 продувка расплава сбоку (а не
снизу, как в бессемеровском способе получения стали из чугуна). При боковой
продувке воздух поступает непосредственно в рафинируемый расплав, минуя легко
затвердевающую медь, к-рая собирается на дне конвертера. Огромное значение для
массового произ-ва меди имело изобретённое на рубеже 20 в. флотационное
обогащение, позволившее успешно перерабатывать руды с содержанием меди менее 1%. Нефлотирующиеся бедные окисленные руды (менее 0,7% Си) обрабатывают
гидрометаллургич. способом (путём выщелачивания). Сульфидные руды можно
выщелачивать в самом месторождении (без добычи руды), используя способ
интенсификации выщелачивания с применением бактерий (см. Бактериальное
выщелачивание).
Олово в древности выплавляли в простейших шахтных печах, а затем очищали от
посторонних примесей посредством ликвационных и окислит, процессов. Коренные
оловянные руды перед плавкой подвергали дроблению и простейшему обогащению; из
россыпей руду добывали промывкой. В совр. М. в связи с необходимостью
использования бедных оловянных руд со значит, содержанием примесей (сера,
мышьяк, сурьма, висмут, серебро и др.) олово получают по сложным схемам
комплексной переработки руд, к-рые включают в себя обогащение, обжиг,
выщелачивание примесей из рудных концентратов, магнитную сепарацию их,
восстановит, плавку в отражат., шахтных или электрич. (лучший способ) печах с
получением чернового олова и рафинирование его гл. обр. пирометаллургич.
(иногда электролитич.) методом.
Первые способы произ-ва ртути сводились, по-видимому, к обжигу руды в кучах;
ртуть конденсировалась при этом на холодных предметах. Позднее появилась
керамич. реторта. Методы получения ртути, описанные нем. учёным Г. Агриколой
(16 в.), сводятся к обжигу руды в керамич. сосудах с различными
конденсаторами. Железные реторты появились в 17 в. (1641). Затем по мере роста
спроса на ртуть получили применение более производит, шахтные печи (периодич.,
а позднее и непрерывного действия), отражат. печи (с 1842), трубчатые
вращающиеся печи (с нач. 20 в.), к-рые служат осн. агрегатом для переработки
ртутных руд. Перспективный способ получения ртути - переработка руд в кипящего
слоя печах, успешно освоенная в СССР.
Технологич. схемы процессов получения остальных металлов, произ-во к-рых
достигло значит, уровня только в течение последних столетий (а иногда и лет),
освещаются в соответствующих статьях (см. Алюминий, Цинк, Марганец, Хром,
Никель, Магний и др.).
Совр. М. как совокупность осн. технологич. операций произ-ва металлов и
сплавов включает в себя: 1) подготовку руд к извлечению металлов (в т. ч.
обогащение); 2) процессы извлечения и рафинирования металлов:
пирометаллургические, гидрометаллургические, электролитические; 3) процессы
получения изделий из металлич. порошков путём спекания; 4) кристаллофизические
методы рафинирования металлов и сплавов; 5) процессы разливки металлов и
сплавов (с получением слитков или отливок); 6) обработку металлов давлением; 7)
термическую, термомеханическую, химико-термическую и др. виды обработки
металлов для придания им соответствующих свойств; 8) процессы нанесения
защитных покрытий.
С М. тесно связаны коксохимическая промышленность, производство огнеупоров
и ряд др. отраслей пром-сти.
Подготовка руд к извлечению металлов начинается с дробления, измельчения,
грохочения и классификации (см. Классификатор). Следующая стадия
обработки - обогащение (см. Обогащение полезных ископаемых). В процессе
обогащения или после него материалы подвергают обычно обжигу или сушке.
Весьма перспективен обжиг в кипящем слое. Наибольшее применение в
обогатительной технике имеют флотационные, гравитационные, магнитные и
электрич. методы. Флотационными процессами перерабатывают более 90% всех
обогащаемых руд цветных и редких металлов. Из гравитац. процессов
распространены обогащение в тяжёлых средах, отсадка, концентрация на столах и
др. методы.
Большое значение обогатит, процессов в совр. М. обусловлено стремлением к
повышению эффективности металлургич. произ-ва, а также тем, что по мере роста
выплавки металлов приходится использовать всё более бедные руды. Непосредств.
металлургич. переработка таких руд (без обогащения), как правило, неэкономична,
а в нек-рых случаях даже невозможна.
Заключит, операциями подготовки руд являются обычно их усреднение, смешение,
а также окускование посредством агломерации, окатывания (окомкования)
или брикетирования. Необходимость окускования обусловлена тем, что в
процессе обогащения руды подвергаются измельчению, а применение в плавке мелко
измельчённых материалов в нек-рых металлургич. произ-вах нежелательно или
недопустимо.
Пирометаллургические (высокотемпературные) методы извлечения и рафинирования
металлов весьма многообразны (см. Пирометаллургия). Они осуществляются в
шахтных, отражат. или электрич. печах, конвертерах и др. агрегатах. В пирометаллургич.
процессах происходит концентрирование металлов и удаляемых примесей в различных
фазах системы, образующейся при нагреве или расплавлении перерабатываемых
материалов. Такими фазами могут служить газ, жидкие металлы, шлак, штейн и
твёрдые вещества. После разделения одна или неск. из этих фаз направляются на
дальнейшую переработку. Для осуществления необходимых операций в
пирометаллургии применяют окислит., восстановит, и др. процессы. С целью
интенсификации окисления успешно используют газообразный кислород, а также хлор
и селитру. В качестве восстановителей применяют углерод, окись углерода,
водород или нек-рые металлы (см. Металлотермия). Примерами восстановит,
процессов могут служить доменная плавка, выплавка вторичной меди, олова и
свинца в шахтных печах, получение ферросплавов и титанового шлака в
рудовосстановит. электропечах. Магнийтермич. восстановлением получают, напр.,
титан. Окислит, рафинирование является необходимым элементом в мартеновском и
конвертерном произ-ве стали, при получении анодной меди, а также свинца.
Весьма широко используются методы извлечения и рафинирования металлов,
основанные на образовании сульфидов, хлоридов, иодидов (см. Иодидный метод),
карбонилов. Большое значение имеют процессы, базирующиеся на явлениях испарения
и конденсации (дистилляция, ректификация, вакуумная сепарация,
сублимация).
Получили развитие внепечные методы рафинирования стали, а также вакуумная
плавка и плавка в аргоне, находящие применение при производстве химически
активных металлов (титана, циркония, молибдена и др.) и стали.
Гидрометаллургические методы извлечения и рафинирования металлов, не
требующие высоких темп-р, базируются на использовании водных растворов (см.
Гидрометаллургия).
Чтобы перевести металлы в раствор, применяют выщелачивание с помощью водных
растворов кислот, оснований или солей. Для выделения элементов из раствора
используют цементацию, кристаллизацию, адсорбцию, осаждение (см. Осадителъная
плавка) или гидролиз. Широкое распространение получили сорбция металлов
ионообменными веществами (в основном синтетич. смолами) и экстракция (с
помощью органич. жидкостей). Совр. сорбционные и экстракционные процессы
характеризуются высокой эффективностью. Они позволяют извлекать металлы не
только из растворов, но и из пульпы, минуя операции отстаивания, промывки и
фильтрации. Из др. гидрометаллургич. процессов следует отметить автоклавную
переработку материалов при повыш. темп-pax и давлениях (см. Автоклав), а
также очистку растворов от примесей в кипящем слое. В нек-рых произ-вах применяют
извлечение металлов (напр., золота) из руд с помощью ртути - амальгамацию.
Большое значение в М. имеет получение или рафинирование цветных металлов
электролитическим осаждением (см. Электролиз) как из водных растворов
(медь, никель, кобальт, цинк), так и из расплавов (алюминий, магний). Алюминий,
напр., получают электролизом криолитглинозёмного расплава.
Находит применение также производство изделий из металлических
порошков, или порошковая металлургия. В ряде случаев этот процесс
обеспечивает более высокое качество изделий и лучшие технико-экономич.
показатели произ-ва, чем традиционные способы.
Для получения особо чистых металлов и полупроводников применяются кристаллофизические методы рафинирования
(зонная плавка, вытягивание монокристаллов
из расплава), основанные на различии составов твёрдой и жидкой фаз при
кристаллизации металла из расплава.
Процессы получения отливок из расплавл. металлов и сплавов (см.
Литейное производство) и слитков, предназнач. для последующей обработки давлением
(см. Разливка металла), известны человечеству на протяжении мн. веков.
Осн. направления технич. прогресса в этой области связаны с переходом к
непрерывной разливке стали и сплавов и к совмещённым процессам литья и
обработки заготовок давлением (напр., бесслитковое получение проволоки или
листа из расплавл. алюминия, меди, цинка).
Обработка металлов давлением также известна людям очень давно (ковка железа
была, напр., необходимым элементом процесса переработки крицы). Кузнечно-штамповочное
производство и прессование являются важнейшими составными частями
машиностроения. Прокатка - основной способ обработки металлов и сплавов
давлением на совр. металлургич. з-дах (см. Прокатное производство). Прокатный
стан, впервые предложенный, по-видимому, ещё Леонардо да Винчи (1495),
превратился в мощный высокоавтоматизиров. агрегат, производительность к-рого
достигает неск. млн. т металла в год. Наряду с листовым и сортовым
металлом с помощью прокатных станов получают трубы, гнутые и периодические
профили (см. Прокатный профиль), биметалл и др. виды изделий. Для
изготовления проволоки в совр. М. широко применяют волочение.
Термическая обработка, обеспечивающая получение наиболее благоприятной
структуры металлов и сплавов, также имеет весьма древнее происхождение. Такие
процессы, как цементация, закалка, отжиг и отпуск металлов, были
известны и хорошо освоены на практике уже в глубокой древности. Науч. основы термической
обработки металлов и сплавов были разработаны Д. К. Черновым (см.
Металловедение).
В совр. технике термич. обработка металлов и сплавов, а также др. виды
обработки (см. Термомеханическая обработка, Химико-механическая обработка,
Химико-термическая обработка) имеют очень широкое применение. Кроме готовых
деталей, к-рые подвергаются обработке на маш.-строит, предприятиях, её проходят
мн. виды продукции и на металлургич. з-дах. Это относится, напр., к стальным
рельсам (объёмная закалка или закалка головки), к толстым листам и арматурной
стали (упрочняющая обработка), к тонкому листу из трансформаторной стали (отжиг
для улучшения магнитных свойств) и т. д.
Большое значение в совр. М. приобретают процессы нанесения на металл
различных защитных покрытий. К таким процессам относятся лужение,
цинкование, нанесение пластмассовых и др. покрытий, значительно повышающих
качество и срок службы металла.
Значение М. в создании совр. цивилизации исключительно велико. Материальная
культура человеческого общества немыслима без металлов; она базируется на них в
произ-ве средств произ-ва, средств транспорта и связи, в стр-ве, в воен. деле.
Большую роль играют металлы в с. х-ве и в произ-ве предметов потребления.
Данные об объёме и динамике произ-ва стали, чугуна, важнейших цветных металлов
и др. сведения о М. как отрасли пром-сти приведены в статьях Чёрная
металлургия, Цветная металлургия.
Лит.:
Основы металлургии, т. 1 - 6, М., 1961 - 73; Металловедение и
термическая обработка стали. Справочник, 2 изд., М., 1961-62; Прокатное
производство. Справочник, т. 1 - 2, М., 1962; Доменное производство.
Справочник, т. 1-2, М., 1963; Сталеплавильное производство. Справочник, т. 1 - 2, М., 1964; Aitchison L., A history of metals, v.
1-2, L., 1960.
А. Я.
Стомахин.
"МЕТАЛЛУРГИЯ", центральное издательство Гос. комитета
Совета Министров СССР по делам издательств, полиграфии и книжной торговли,
выпускающее литературу по чёрной и цветной металлургии. Осн. в 1939 в Москве
как Металлургиздат, с 1963-"М.". Издаёт научно-технич.,
производственно-технич., справочную, учебную и др. лит-ру, а также каталоги,
плакаты; 7 журналов, в т. ч. "Сталь", "Цветные металлы" и
др. В 1973 книжная продукция издательства составила 207 названий тиражом 1,7
млн. экз., объёмом 21 400 тыс. печатных листов-оттисков.
В. П. Адрианова.
МЕТАЛЛЫ, простые вещества, обладающие в обычных условиях характерными
свойствами: высокой электропроводностью и теплопроводностью, отрицательным
температурным коэффициентом электропроводности , способностью хорошо отражать
электромагнитные волны (блеск и непрозрачность), пластичностью. М. в твёрдом
состоянии имеют кристаллич. строение. В парообразном состоянии М. одноатомны.
Перечисленные выше характерные свойства М. обусловлены их электронным
строением. Атомы М. легко отдают внешние (валентные) электроны. В кристаллич.
решётке М. не все электроны связаны со своими атомами. Нек-рая их часть ( ~ 1
на атом) подвижна. Эти электроны могут более или менее свободно перемещаться по
М. Существование свободных электронов (электронов проводи мости) в М.
объясняется зонной теорией (см. Твёрдое тело). М. можно представить себе
в виде остова из положительных ионов, погружённого в "электронный
газ". Последний компенсирует силы электростатич. отталкивания между
положительными ионами и тем самым связывает их в твёрдое тело (металлическая
связь).
Из известных (1974) 105 хим. элементов 83- М. и лишь 22 - неметаллы. Если
в длинном или "полудлинном" варианте периодической системы элементов Менделеева
провести прямую линию от бора до астата (табл. 1), то можно считать, что
неметаллы расположены на этой линии и справа от неё, а М. - слева.
Не следует, однако, абсолютизировать ни свойства, характерные для М., ни их
отличия от неметаллов. Металлич. блеск присущ только компактным металлич.
образцам. Тончайшие листки Ag и Аи (толщиной 10-4 мм) просвечивают
голубовато-зелёным цветом. Мельчайшие порошки М. часто имеют чёрный или
черно-серый цвет. Нек-рые металлы (Zn, Sb, Bi) при комнатной темп-ре хрупки и
становятся пластичными только при нагревании.
ПЕРИОДИЧЕСКАЯ СИСТЕМА ЭЛЕМЕНТОВ Д.И.МЕНДЕЛЕЕВА свойства металлов
Вся совокупность перечисленных выше свойств присуща типичным М. (напр., Сu, Аu, Ag, Fe) при обычных условиях (атм. давлении,
комнатной темп-ре). При очень высоких давлениях (~-105-10" am)
свойства М. могут существенно измениться, а неметаллы приобрести металлич.
свойства.
Многие простые вещества по одним свойствам можно отнести к М., по др.-к
неметаллам. Особенно много такого рода "нарушений" имеет место вблизи
границы, проведённой в табл. 1. Так, Ge по внешнему виду-М., в хим. отношении
проявляет себя скорее как М. (легче отдаёт электроны, чем принимает), а по
величине и характеру электропроводности Ge - полупроводник. Сурьма Sb имеет
электросопротивление слишком большое для М., однако температурный коэфф.
сопротивления у Sb положительный и большой, как у М.; по способности отдавать
электроны Sb также относится к М. As, 5Ьи Bi иногда наз. полуметаллами. Ро
по внешнему виду- М., в хим. отношении ему присущи свойства и М., и неметалла -
наряду с положительной валентностью (точнее окислительным числом) проявляется и
отрицательная (-2).
Металлич. сплавы по свойствам имеют много общего с М., поэтому в физической,
технической и экономической литературе нередко к М. относят также и сплавы.
Историческая справка. Термин "металл" произошёл от греч. слова
metallon (от metalleuo - выкапываю, добываю из земли), к-рое означало
первоначально копи, рудники (в этом смысле оно встречается у Геродота, 5 в.
до н. э.). То, что добывалось в рудниках, Платон называл metalleia. В древности
и в ср. века считалось, что существует только 7 М.: золото, серебро, медь,
олово, свинец, железо, ртуть (см. Знаки химические). По алхимич.
представлениям, М. зарождались в земных недрах под влиянием лучей планет и
постепенно крайне медленно совершенствовались, превращаясь в серебро и золото
(см. Алхимия). Алхимики полагали, что М.- вещества сложные, состоящие из
"начала металличности" (ртути) и "начала горючести"
(серы). В нач. 18 в. получила распространение гипотеза, согласно к-рой М.
состоят из земли и "начала горючести" - флогистона. М. В. Ломоносов насчитывал
6 М. (Au, Ag, Си, Sn, Fe, Pb) и определял М. как "светлое тело, которое
ковать можно". В кон. 18 в. А. Л. Лавуазье опроверг гипотезу флогистона и
показал, что М.- простые вещества. В 1789 Лавуазье в руководстве по химии дал
список простых веществ, в к-рый включил все известные тогда 17 М. (Sb, Ag, As,
Bi, Co, Cu, Sn, Fe, Mn, Hg, Mo, Ni, Au, Pt, Pb, W, Zn). По мере развития
методов хим. исследования число известных М. возрастало. В 1-й пол. 19 в. были
открыты спутники Pt, получены путём электролиза нек-рые щелочные и щёлочноземельные
М., положено начало разделению редкоземельных металлов, открыты неизвестные М.
при хим. анализе минералов. В 1860-63 методом спектрального анализа были
открыты Cs, Rb, Tl, In. Блестяще подтвердилось существование М., предсказанных
Д. И. Менделеевым на основе его периодич. закона. Открытие радиоактивности в
кон. 19 в. повлекло за собой поиски природных радиоактивных М., увенчавшиеся
полным успехом. Наконец, методом ядерных превращений начиная с сер. 20 в. были
искусственно получены радиоактивные М., в частности трансурановые элементы.
В конце 19 - нач. 20 вв. получила физико-хим. основу металлургия -наука о
произ-ве М. из природного сырья. Тогда же началось исследование свойств М. и их
сплавов в зависимости от состава и строения (см. Металловедение,
Металлофизика).
Химические свойства. В соответствии с местом, занимаемым в периодич. системе
элементов (табл. 1), различают М. главных и побочных подгрупп. М. главных
подгрупп (подгруппы а) наз. также непереходными. Эти М. характеризуются тем,
что в их атомах происходит последовательное заполнение s-и р-электронных
оболочек. В атомах М. побочных подгрупп (подгруппы б), наз. переходными,
происходит достраивание d- и f-оболочек, в соответствии с чем их
делят на d-rpynny и две f-группы - лантаноиды и актиноиды. В подгруппы а входят 22 М.: Li, Na, К, Rb, Cs, Fr (I a); Be, Mg, Ca, Sr, Ba,
Ra (II a); Al, Ga, In, Tl (III a); Ge, Sn, Pb (IV a); Sb, Bi (V
a);
Po (VI а).
В подгруппы б входят: 1)
33 переходных металла d-группы [Си, Ag, Au (I б); Zn, Cd,
Hg (II б); Sc, Y, La,
Ac (III 6); Ti, Zr, Hf\ Ku (IV 6); V, Nb, Та, элемент с Z = 105 (V 6); Cr, Mo, W (VI б); Mn, Тс, Re (VII 6); Fe, Co, Ni, Ru, Rh, Pd, Os, Ir, Pt (VIII 6)]; 2)
28 M. f-группы (14 лантаноидов и 14 актиноидов).
Электронная структура атомов некоторых d-элементов имеет ту особенность, что
один из электронов внешнего уровня переходит на d-подуровень. Это происходит
при достройке этого подуровня до 5 или 10 электронов. Поэтому электронная
структура валентных подуровней атомов d-элементов, находящихся в одной
подгруппе, не всегда одинакова. Напр.,СгиМо (подгруппа VI б) имеют внешнюю
электронную структуру соответственно 3d54s' и 4rf55s',
тогда как у W она 5d46s2. В атоме Pd (подгруппа VIII б)
два внешних электрона "перешли" на соседний валентный подуровень, и
для атома Pd наблюдается d'° вместо ожидаемого d8s2.
М. присущи многие общие хим. свойства, обусловленные слабой связью валентных
электронов с ядром атома: образование положительно заряженных ионов (катионов),
проявление положительной валентности (окислительного числа), образование
основных окислов и гидроокисей, замещение водорода в кислотах и т. д. Металлич.
свойства элементов можно сравнить, сопоставляя их электроотрицательность
[способность атомов в молекулах (в ковалентной связи) притягивать электроны,
выражена в условных единицах]; элементу присущи свойства М. тем больше, чем
ниже его электроотрицательность (чем сильнее выражен электроположительный
характер).
В периодической системе элементов Менделеева (табл. 1) в пределах каждого
периода, начиная со 2-го, с увеличением ат. н. электроотрицательность
возрастает от 2 до 7, начиная со щелочного металла и кончая галогеном (переход
от М. к неметаллам). В пределах подгрупп (а и б) с увеличением ат. н.
электроотрицательность в общем уменьшается, хотя и не всегда последовательно. В
семействах лантаноидов и актиноидов она сохраняется примерно на одном уровне.
Если расположить М. в последовательности увеличения их нормальных
потенциалов, получим т. н. ряд напряжений или ряд активностей (табл.
2 и 3). Рассмотрение этого ряда показывает, что по мере приближения к его концу
- от щелочных и щёлочноземельных М. к Pt и Au - электроположительный характер
членов ряда уменьшается. М. от Li по Na вытесняют Н2 из Н2О
на холоду, а от Mg по Т1 - при нагревании. Все М., стоящие в ряду выше H2,
вытесняют его из разбавл. кислот (на холоду или при нагревании). М., стоящие
ниже Н2, растворяются только в кислородных кислотах (таких, как
концентрир. H2SO4 при нагревании или HNO3), a Pt, Au
-только в царской водке (Ir нерастворим и в ней).
М. от Li no Na легко реагируют с О2 на холоду; последующие члены
ряда соединяются с О2 только при нагревании, a Ir, Pt, Au в прямое
взаимодействие с О2 не вступают.
Окислы М. от Li no A1 (табл. 2) и от La no Zn (табл. 3) трудно восстановимы;
по мере продвижения к концу ряда восстановимость окислов увеличивается, а
окислы последних его членов разлагаются на М. и О2 уже при слабом
нагревании. О прочности соединений М. с кислородом (и др. неметаллами) можно
судить и по разности их электроотрицательностей (табл. 1): чем она больше, тем
прочнее соединение.
Табл. 2. -Нормальные электродные потенциалы непереходных металлов
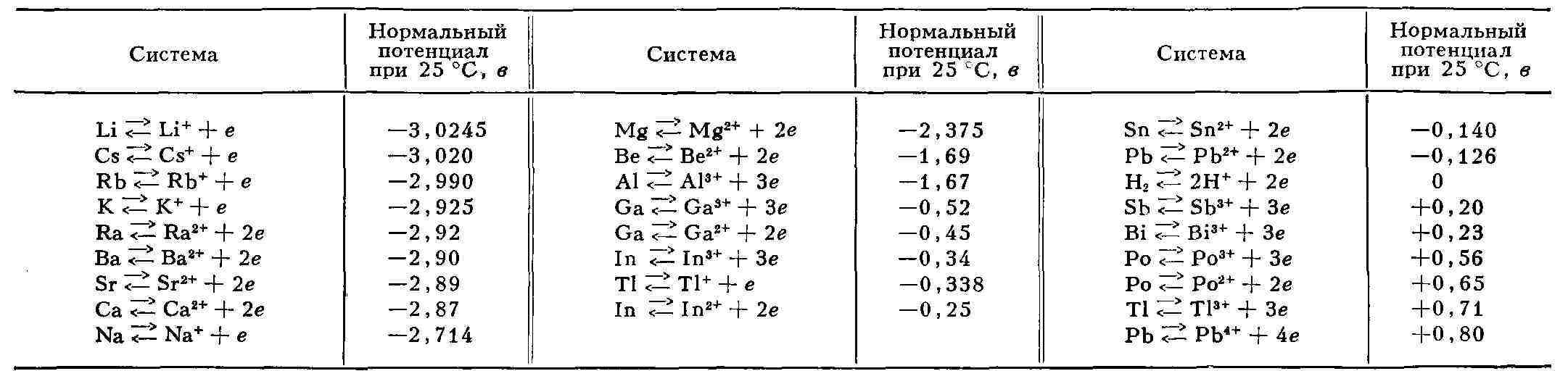
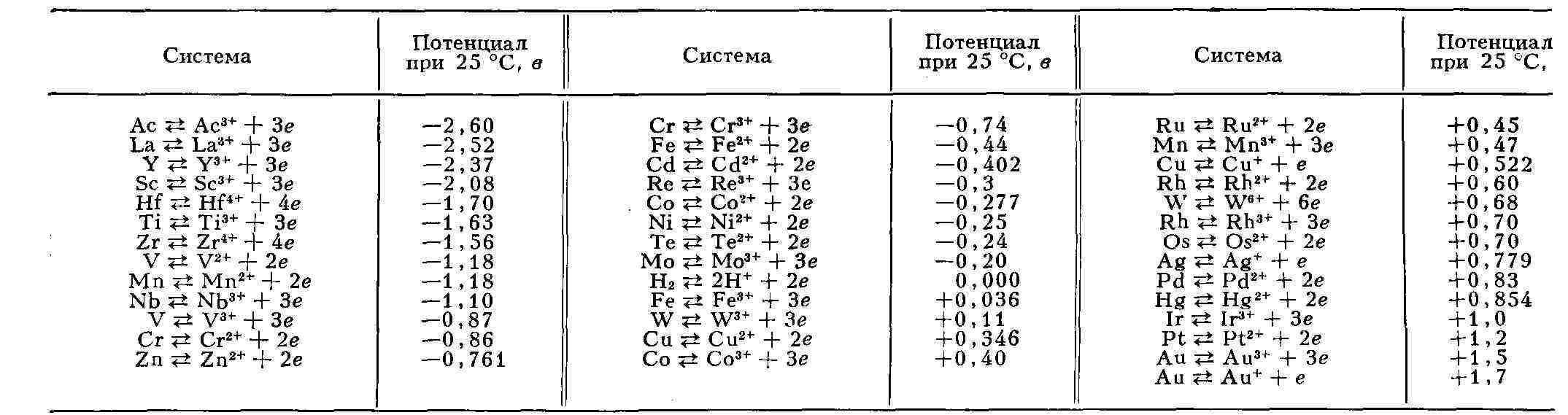
Валентности (точнее, окислит, числа) непереходных М. равны: +1 для подгруппы
1а; +2 для Па; +1 и +3 для Ilia; +2 и +4 для IVа; +2, +3 и + 5
для Va; -2, +2, + 4, +6 для VI а. У переходных М. наблюдается ещё
большее разнообразие окислительных чисел: + 1, +2, +3 для подгруппы I 6; +2
для II б; + 3 для III 6; +2, +3, +4 для IV б; +2, +3, +4,
+5 для V 6; + 2, +3, +4, +5, +6 для VI б; +2, + 3, +4, +5, +6, +7
для VII б; от +2 до +8 в VIII б. В семействе лантаноидов наблюдаются
окислительные числа +2, + 3 и +4, в семействе актиноидов -от +3 до +6. Низшие
окислы М. обладают основными свойствами, высшие являются ангидридами кислот
(см. Кислоты и основания). М., имеющие переменную валентность (напр.,
Cr, Mn, Fe), в соединениях, отвечающих низшим степеням окисления [Сr( + 2), Мn
( + 2), Fe ( + 2)], проявляют восстановительные свойства; в высших степенях
окисления те же М. [Сr ( + 6), Мn ( + 7), Fe ( + 3)] обнаруживают окислительные
свойства. О хим. соединениях М. друг с другом см. в ст. Металлиды, о соединениях
М. с неметаллами см. в статьях Бориды, Гидриды, Карбиды, Нитриды, Окислы и
др.
Лит.:
Некрасов Б. В., Основы общей химии, 2 изд., т. 1 - 3, М., 1969
- 70; Дей М. К., Селбин Дж., Теоретическая неорганическая химия, пер. с англ.,
2 изд., М., 1971; Барнард А., Теоретические основы неорганической химии, пер. с
англ., М., 1968; Рипан Р., Ч е тяну И., Неорганическая химия, т. 1 - 2, Химия
металлов, пер. с рум., М., 1971 - 72. См. также лит. при ст. Неорганическая
химия.
С. А. Погодин.
Физические свойства. Большинство М. кристаллизуется в относительно простых
структурах - кубических (кубические объёмноцентрированная ОЦК и
гране-центрированная ГЦК решётки) и гексагональных ПГУ, соответствующих
наиболее плотной упаковке атомов. Лишь небольшое число М. имеет более сложные
типы кристаллич. решёток. Многие М. в зависимости от внешних условий (темп-ры,
давления) могут существовать в виде двух или более кристаллич. модификаций (см.
Полиморфизм). Полиморфные превращения иногда связаны с потерей металлич.
свойств, напр, превращение белого олова ((З-Sn) в серое (a-Sn).
Электрические свойства. Удельная электропроводность М. при комнатной темп-ре
а~10~6-10~4 ом~1 см~1 (табл.
1), тогда как у диэлектриков, напр, у серы, a~ 10~17 ом~1см~1.
Промежуточные значения а соответствуют полупроводникам. Характерным
свойством М. как проводников электрич. тока является линейная зависимость между
плотностью тока и напряжённостью приложенного электрич. поля (Ома закон). Носителями
тока в М. являются электроны проводимости, обладающие высокой подвижностью.
Согласно квантово-механич. представлениям, в идеальном кристалле электроны
проводимости (при полном отсутствии тепловых колебаний кристаллической
решётки) вообще не встречают сопротивления на своём пути. Существование у
реальных М. электросопротивления является результатом нарушения периодичности
кристаллич. решётки. Эти нарушения могут быть связаны как с тепловым движением
атомов, так и с наличием примесных атомов, вакансий, дислокаций и
др. дефектов в кристаллах. На тепловых колебаниях и дефектах (а также
друг на друге) происходит рассеяние электронов. Мерой рассеяния служит длина
свободного пробега - среднее расстояние между двумя последовательными
столкновениями электронов. Величина удельной электропроводности а связана с
длиной свободного пообега / соотношением:

где п - концентрация электронов проводимости (~1022-1023
см~3), е - заряд электрона, рр = 2лН (Зи/8я)'/а
- граничный фермиевский импульс (см. Ферми поверхность), h - Планка
постоянная. Зависимость а или удельного электросопротивления р от
темп-ры Т связана с зависимостью I от Т. При комнатных
темп-рах в М. / ~ 10~6 см.
При темп-рах, значительно превышающих Дебая температуру, сопротивление
р обусловлено гл. обр. тепловыми колебаниями кристаллической решётки и
возрастает с темп-рой линейно:
Р = рост(1+аГ). (2) Постоянная а наз. температурным коэффициентом
электропроводности и имеет при темп-ре Т = О С типичное значение a
=4-10~3 град"1. При более низких темп-рах,
когда влиянием тепловых колебаний атомов на рассеяние электронов можно
пренебречь, сопротивление практически перестаёт зависеть от темп-ры.
Это предельное значение сопротивления наз. остаточным. Величина рост
характеризует концентрацию дефектов в решётке М. Удаётся получить столь чистые
(сверхчистые) и свободные от дефектов М., что их остаточное сопротивление в 104—105
раз превышает сопротивление этих М. в обычных условиях. Длина свободного
пробега электронов в сверхчистых М. l ~ 10-2 см. Теоретич.
рассмотрение показывает, что при низких темп-pax формула для удельного
электросопротивления имеет вид:
р = рост + AT2 + ВT5, (3)
где А и В — величины, не зависящие от Т. Член ВТ5
связан с рассеянием электронов на тепловых колебаниях атомов, а член AT2
— со столкновениями электронов друг с другом и даёт заметный вклад в
сопротивление лишь у нек-рых М., напр, у Pt. Однако закономерность (3)
выполняется лишь приближённо.
У нек-рых М. и металлидов при определённой темп-ре, наз. критической,
наблюдается полное исчезновение сопротивления — переход в сверхпроводящее
состояние (см. Сверхпроводимость). Критич. темп-ры чистых металлов лежат
в интервале от сотых долей К до 9 К (табл. 1).
Если металлич. образец, по к-рому течёт ток, поместить в постоянное
магнитное поле, то в М. возникают явления, обусловленные искривлением
траекторий электронов в магнитном поле в промежутке между столкновениями (гальваномагнитные
явления). Среди них важное место занимают Холла эффект и изменение
электросопротивления М. в магнитном поле (магнетосопротивление). Влияние
магнитного поля тем больше, чем больше длина свободного пробега l, т. е.
чем ниже темп-pa и чем меньше примесей в М. При комнатной темп-ре магнитное
поле 107—105 э изменяет сопротивление М. лишь на доли %.
При Т =< 4 К в сверхчистых М. сопротивление может измениться во много
раз. Зависимость электросопротивления М. от внешнего магнитного поля
существенно зависит от характера энергетич. спектра электронов, в частности от
формы поверхности Ферми. У многих металлич. монокристаллов (Au, Cu, Ag и
др.) наблюдается сложная анизотропия сопротивления в магнитном поле.
В магнитных полях ~ 104—105 э и при низких темп-pax у
всех металлич. монокристаллов наблюдается осциллирующая зависимость
электросопротивления от магнитного поля (Шубникова — де Хааза эффект). Это
явление - следствие квантования движения электронов в плоскости, перпендикулярной
направлению магнитного поля. Как правило, квантовая осциллирующая зависимость в
виде небольшой "ряби" наложена на обычную зависимость сопротивления
от магнитного поля.
При нагревании М. до высоких темп-р наблюдается "испарение"
электронов с поверхности М. (термоэлектронная эмиссия). Число
электронов, вылетающих в единицу времени, определяется законом: п ~ eхр
(-ф/kT), где k - Больцмана постоянная, ф - работа выхода электронов
из М. (см. Ричардсона формула). Величина ф различна у разных М. и
зависит также от состояния поверхности. Эмиссия электронов с поверхности М.
происходит также под действием сильных электрич. полей ~ 10 в степени 7 в/см
в результате туннельного просачивания электронов через сниженный полем
потенциальный барьер (см. Туннельная эмиссия). В М. наблюдаются явления фотоэлектронной
эмиссии, вторичной электронной эмиссии и ионно-электронной эмиссии. Перепад
темп-ры вызывает в М. появление электрич. тока или разности потенциалов (см.
Термоэлектрические явления).
Тепловые свойства. Теплоёмкость М. (табл.1) обусловлена как ионным
остовом (решёточная теплоёмкость Ср), так и электронным газом (электронная
теплоёмкость Сэ). Хотя концентрация электронов проводимости в М.
очень велика (см. выше) и не зависит от темп-ры, электронная теплоёмкость мала
и у большинства М. наблюдается только при темп-pax ~ неск. К. Возможность
измерения Сэ связана с тем, что при уменьшении темп-ры Ср
убывает пропорционально Т3, а Сэ ~ Т. Для
Сu: С9 = 0,9-10-4RT, для Pd: Сэ = =
1,6*10~3КТ (R - газовая постоянная). Теплопроводность М.
осуществляется гл. обр. электронами проводимости. Поэтому между удельными
коэфф. электропроводности и теплопроводности существует простое соотношение,
наз. Видемана - Франца законом.
Взаимодействие М. с электромагнитными полями. Переменный электрич. ток при
достаточно высокой частоте течёт по поверхности М., не проникая в его толщу
(см. Скин-эффект). Электромагнитное поле частоты со проникает в М. лишь

глощается незначит. часть электромагнитной энергии. Основная часть энергии
переизлучается электронами проводимости и отражается (см. Металлооптика). В
чистых М. при низких темп-рах длина свободного пробега электронов часто
превышает глубину о. При этом напряжённость поля существенно изменяется
-на длине свободного пробега, что проявляется в характере отражения
электромагнитных волн от поверхности М. (аномальный скин-эффект).
Сильное постоянное магнитное поле существенно влияет на электродинамич.
свойства М. В М., помещённых в такое поле, при условии, если частота электромагнитного
поля кратна частоте прецессии электронов проводимости вокруг силовых линий
постоянного магнитного поля, наблюдаются резонансные явления (см.
Циклотронный резонанс). При определённых условиях в толще М., находящегося в постоянном
магнитном поле, могут распространяться слабо затухающие электромагнитные волны,
т. е. исчезает скин-эффект. Электродинамич. свойства М., помещённого в
магнитное поле, сходны со свойствами плазмы в магнитном поле и являются
одним из основных источников информации об электронах проводимости.
Для электромагнитных волн оптич. диапазона М., как правило, практически
непрозрачны и обладают характерным блеском (см. Отражение света, Зеркало). В
поглощении света в видимом и ультрафиолетовом диапазонах нек-рую роль играет
внутренний фотоэффект. Отражение от поверхности М. плоскополяризованного
света, падающего под произвольным углом, сопровождается поворотом плоскости
поляризации и появлением эллиптич. поляризации (см. Вращение плоскости
поляризации). Это явление используется для определения оптич. констант М.
Общая структура характеристических рентгеновских спектров М. и диэлектриков
одинакова. Тонкая же структура линий, соответствующая квантовым переходам
электронов из зоны проводимости на глубокие уровни, отражает распределение
электронов проводимости по уровням энергии.
Магнитные свойства. Переходные металлы с недостроенными f- и
d-электронными оболочками являются парамагнетиками. Некоторые из них при
определённых температурах переходят в магнитоупорядоченное состояние (см.
Магнетизм, Ферромагнетизм, Антиферромагнетизм, Кюри точка). Магнитное упорядочение
существенно влияет на все свойства М., в частности на электрич. свойства: в
электросопротивление вносит вклад рассеяние электронов на колебаниях магнитных
моментов. Гальваномагнитные явления при этом также приобретают специфич. черты.
Магнитные свойства остальных М. определяются электронами проводимости, к-рые
вносят вклад в диамагнитную и парамагнитную восприимчивости М., и диамагнитной
восприимчивостью ионного состава (см. Диамагнетизм, Парамагнетизм). Магнитная
восприимчивость X большинства М. относительно мала (X ~ 10-6) и
слабо зависит от темп-ры.
При низких темп-pax Г и в больших магнитных полях Н > 104
kT у всех металлич. монокристаллов наблюдается сложная осциллирующая
зависимость суммарного магнитного момента от поля Н (см. Де Хааза -
ван Альфена эффект), природа к-poro та же, что и у эффекта Шубникова - де
Хааза. Исследование осцилляционных эффектов позволяет определить форму
поверхности Ферми.
М. И. Каганов.
Механические свойства. Многие М. обладают комплексом механич. свойств,
обеспечивающим их широкое применение в технике, в частности в качестве конструкционных
материалов. Это, в первую очередь, сочетание высокой пластичности со
значит, прочностью и сопротивлением деформации, причём соотношение этих
свойств может регулироваться в большом диапазоне с помощью механич. и термич.
обработки М., а также получением сплавов различного состава.
Исходной характеристикой механич. свойств М. является модуль упругости G,
определяющий сопротивление кристал-лич. решётки упругому деформированию и
непосредственно отражающий величину сил связи в кристалле. В монокристаллах эта
величина, как и остальные механические характеристики, анизотропна и
коррелирует с темп-рой плавления М. (напр., средний модуль сдвига G изменяется
от 0,18 -10" эрг/см3 для легкоплавкого Na до 27-10"
эрг/см3 для тугоплавкого Re).
Сопротивление разрушению или пластич. деформации идеального кристалла ~ 10~4
G. Но в реальных кристаллах эти характеристики, как и все механич. свойства,
определяются наличием дефектов, в первую очередь дислокаций. Перемещение
дислокаций по плот-ноупакованным плоскостям приводит к элементарному акту
скольжения - основному механизму пластической деформации М. Др. механизмы (двойникование
и сбросообразование) существенны только при пониженных темп-pax. Важнейшая
особенность М.- малое сопротивление скольжению дислокации в бездефектном
кристалле. Это сопротивление особенно мало в кристаллах с чисто металлич.
связью, к-рые обычно имеют плотноупакованные структуры (гранецентрированную
кубическую или гексагональную). В М. с ковалентной компонентой межатомной
связью, имеющих объёмноцентрир. решётку, сопротивление скольжению неск. больше,
однако всё же мало по сравнению с чисто ковалентными кристаллами. Сопротивление
пластической деформации, по крайней мере в М. с гранецентрир. кубической и
гексагональной решётками, связано с взаимодействием движущихся дислокаций с др.
дефектами в кристаллах, с др. дислокациями, примесными атомами, внутренними
поверхностями раздела. Взаимодействие дефектов определяется искажениями решётки
вблизи них и пропорционально G. Для отожжённых монокристаллов начальное
сопротивление пластич. деформации (предел текучести) обычно ~ 10~3-
10~4 G. В процессе деформации число дислокаций в кписталлич. оешётке
(плот-

ине) Это наз. деформационным упрочнением или наклёпом. Для
монокристаллов М. характерно наличие трёх стадий деформационного упрочнения. На
1-й стадии значит, часть дислокаций выходит на поверх-
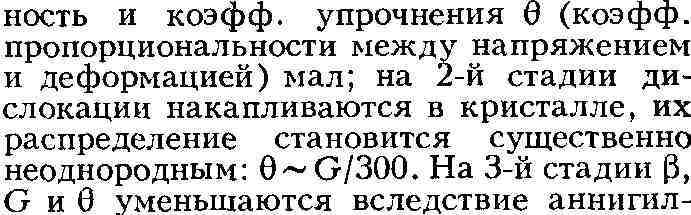
ляции дислокации, выдавливаемых из их плоскостей скольжения. Значение этой
стадии больше для М. с объёмноцентрир. решёткой.
Степень "привязанности" дислокации к плоскости скольжения
определяется шириной дислокации в этой плоскости, к-рая, в свою очередь,
зависит от энер-

дислокации, до 10~4 для сплавов Сu с Широкими дислокациями). Процесс
разрядки дислокационной плотности ускоряется при повышении темп-ры и может
привести к релаксации и значит. восстановлению свойств кристаллов. Чем выше темп-pa и меньше скорость деформирования, тем больше успевают развиться
процессы релаксации и тем меньше деформационное упрочнение.
При Г > 0,5 Гпл в пластин, деформации начинают играть
существенную роль точечные дефекты, в первую очередь вакансии, к-рые, оседая на
дислокациях, приводят к vix выходу из плоскостей скольжения. Если этот процесс
достаточно интенсивен, то деформация не сопровождается упрочнением: М. течёт с
постоянной скоростью при неизменной нагрузке (ползучесть). Протекание
процессов релаксации напряжений и постоянная разрядка дислокационной структуры
обеспечивают высокую пластичность М. при их горячей обработке, что позволяет
придавать изделиям из М. разнообразную форму. Отжиг сильно деформированных
монокристаллов М. нередко приводит к образованию поликристаллов с малой
плотностью дислокаций внутри зёрен (рекристаллизация).
Достижимые степени деформации М. ограничены процессом разрушения. По мере
роста плотности дислокаций при холодной деформации растёт неравномерность их
распределения, приводящая к концентрации напряжений в местах сгущения
дислокаций и зарождению здесь очагов разрушения - трещин. В реальных кристаллах
такие концентрации напряжений имеются и в исходном недеформированном состоянии
(скопление примесей, частицы др. фаз и т. п.). Но вследствие пластичности М.
деформация вблизи опасных мест снимает напряжения и предотвращает разрушение.
Однако, если сопротивление движению дислокаций растёт, то релаксационная
способность материала падает, что под нагрузкой приводит к развитию трещин
(хрупкое разрушение). Это особенно проявляется в М. с объёмноцентрир.
решёткой, в к-рых подвижность дислокаций резко уменьшается при понижении
темп-ры (из-за взаимодействия с примесями и уменьшения числа кристаллографич.
возможных плоскостей скольжения). Предотвращение хладноломкости - одна
из важнейших технич. проблем разработки конструкционных металлических
материалов. Др. актуальная проблема - увеличение прочности и сопротивления
деформации при высоких темп-pax. Зародышами разрушения в этих условиях служат
микропоры, образующиеся в результате скопления вакансий. Эффективный способ
повышения высокотемпературной прочности -уменьшение диффузионной подвижности
точечных дефектов, в частности легированием.
Применяемые в технике конструкционные металлич. материалы являются
поликристаллическими. Их механич. свойства практически изотропны и могут существенно
отличаться от свойств монокристаллов М. Межфазные границы вносят дополнительный
вклад в упрочнение. С др. стороны, они могут быть местами предпочтительного
разрушения (межзёренное разрушение) или деформации. Изменяя число и строение
межфазных границ, форму и пространственное расположение отдельных структурных
составляющих многофазных систем (поликристаллов, гетерофазных агрегатов,
возникающих вследствие фазовых превращений, или искусственно полученных
композиций), а также регулируя состав и дефектную структуру отдельных
кристаллов, можно получить огромное разнообразие механич. свойств, необходимых
для практич. использования металлич. материалов.
А. Л. Ройтбурд.
Лит.:
Френкель Я. И., Введение в теорию металлов, 2 изд., М.- Л.,
1950; Бете Г., Зоммерфельд А., Электронная теория металлов, пер. с нем., М.-
Л.> 1938; Лифшиц И. М., Азбель М. Я., Каганов М. И., Электронная теория
металлов, М., 1971; Абрикосов А. А., Введение в теорию нормальных металлов, М.,
1972; Слэтер Дж., Диэлектрики, полупроводники, металлы, пер. с англ., М., 1969;
Шульце Г., Металлофизика, пер. с нем., М., 1971.
Металлы в технике. Благодаря таким свойствам, как прочность,
твёрдость, пластичность, коррозионная стойкость, жаропрочность, высокая
электрич. проводимость и мн. др., М. играют громадную роль в совр. технике,
причём число М., находящих применение, постоянно растёт. Характерно, что до
нач. 20 в. мн. важнейшие М.- Al, V, W, Мо, Ti, U, Zr и др.- либо не
производились вообще, либо выпускались в очень огранич. масштабах; такие М.,
как Be, Nb, Та, начали сравнительно широко использоваться лишь накануне 2-й
мировой войны 1939-45. В 70-х гг. 20 в. в промышленности применяются
практически все М., встречающиеся в природе.
Все М. и образованные из них сплавы делят на чёрные (к ним относят железо и
сплавы на его основе; на их долю приходится ок. 95% производимой в мире
металлопродукции) и цветные, или, точнее, нежелезные (все остальные М. и
сплавы). Большое число нежелезных М. и широкий диапазон их свойств не позволяют
классифицировать их по к.-л. единому признаку. В технике принята условная
классификация, по к-рой эти М. разделены на неск. групп по различным признакам
(физ. и хим. свойствам, характеру залегания в земной коре), специфичным для той
или иной группы: лёгкие металлы (напр., Al, Mg), тяжёлые М. (Си, РЬ и
др.), тугоплавкие металлы (W, Мо и др.), благородные металлы (Au,
Pt и др.), рассеянные металлы (Ga, In, T1), редкоземельные М. (Sc, Y, La и лантаноиды,
см. Редкоземельные элементы"), радиоактивные металлы (Ra, U и
др.). М., к-рые производят и используют в огранич. масштабах, наз. редкими
металлами. К ним относят все рассеянные, редкоземельные и радиоактивные М.,
большую часть тугоплавких и нек-рые лёгкие М.
Большая способность М. к образованию многочисл. соединений разного типа, к
различным фазовым превращениям создаёт благоприятные условия для получения
разнообразных сплавов, характеризующихся требуемым сочетанием полезных
свойств. Число используемых в технике сплавов превысило уже 10 тыс. Значение
сплавов как конструкционных материалов, электротехнических материалов,
материалов с особыми физ. свойствами (см. Прецизионные сплавы) непрерывно
возрастает. В то же время в связи с развитием полупроводниковой и ядерной
техники расширяется произ-во ряда особо чистых металлов (чистотой, напр.,
99,9999% и выше).
Применение того или иного М. (или сплава) в значит, мере определяется
практич. ценностью его свойств; однако существ, значение имеют и др.
обстоятельства, в первую очередь природные запасы М., доступность и
рентабельность его добычи. Из наиболее ценных и важных для совр. техники М.
лишь немногие содержатся в земной коре в больших количествах: А1 (8,8%), Fe
(4,65%), Mg (2,1%), Ti (0,63%). Природные ресурсы ряда весьма важных М.
измеряются сотыми долями процента (напр., Си, Mn, Cr, V, Zr) и даже тысячными
долями (напр., Zn, Sn, Pb, Ni, Co, Nb). Нек-рые ценные М. присутствуют в земной
коре в ещё меньших количествах. Так, содержание урана — важнейшего источника
ядерной энергии — оценивается в 0,0003%, вольфрама, являющегося основой твёрдых
сплавов,— 0,0001% и т. д. Особенно бедна природа благородными и т. н. редкими
М.
Многообразие М. предопределяет большое число способов их получения и обработки
(см. Металлургия). Взаимосвязь состава, строения и свойств металлов и сплавов,
а также закономерности их изменения в результате теплового, хим. или механич.
воздействия изучает металловедение. О свойствах, способах получения, масштабах
произ-ва и применении отдельных М. см. в статьях, посвящённых соответствующим
химическим элементам и сплавам на их основе (напр., Алюминий, Алюминиевые
сплавы, Бериллий, Бериллиевые сплавы и т. д.).
О применении М. и их сплавов в искусстве см. в статьях Бронза, Железо, Золото,
Медь, Олово, Серебро, Сталь, Чугун, Гравирование, Гравюра, Зернь, Ковка,
Насечка, Тиснение, Филигрань, Чеканка, Ювелирное искусство.
И. И. Новиков.